Putting The Pieces Together: Bisnow's Dec. 10 Event To Explore Modular's Benefits For Healthcare Construction
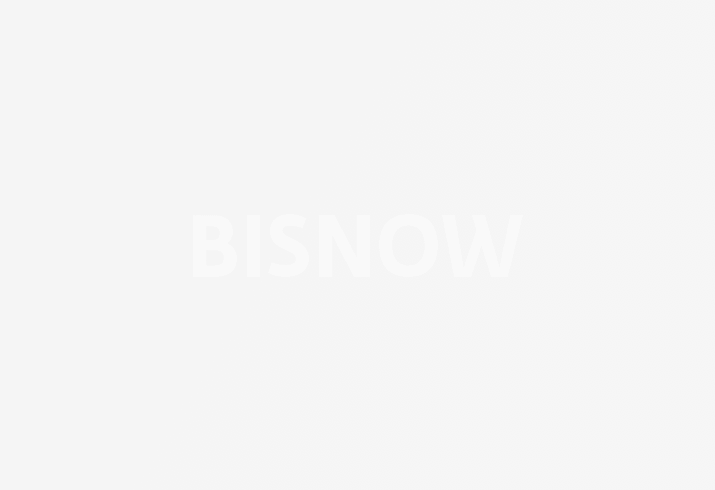
Healthcare facilities seeking to expand or incorporate new technologies are increasingly turning to modular construction to reduce costs, accelerate construction and meet patients’ needs.
Modular construction involves fabricating building components in a factory, then assembling them on-site. The Modular Building Institute estimates that this approach can result in up to 50% faster project completions compared to standard construction techniques.
Architecture and engineering firm EwingCole has applied modular construction techniques in projects with major hospital systems in New York, including the Hospital for Special Surgery and Northwell Health.
EwingCole Managing Principal Mary Frazier will speak on the Future-Proofing Healthcare Spaces Through Modular Construction panel at Bisnow’s New York Healthcare Real Estate Conference on Dec. 10.
Click here to register and purchase tickets.
In a conversation with Bisnow, Frazier discussed how the firm is using modular construction to create healthcare facilities that are equipped for the future needs of patients and providers.
Bisnow: What are some design trends you're noticing in the healthcare industry?
Frazier: We’re discussing how to integrate advanced technologies into our projects and how they impact the care delivered in the future. For example, how might ideas such as artificial intelligence and remote monitoring of patients affect — or not affect — the spaces that we're designing?
We also consider how to make spaces as flexible as possible to accommodate future changes. Utilizing prefabrication and modular systems would allow for easier modifications as needs evolve.
Creating human-centered design and prioritizing the needs and experiences of patients and healthcare providers are top of mind. We know that staff will be in demand, so we aim to create staff areas that offer opportunities for recharge. We also want to make sure that these spaces include enhanced safety and security measures.
EwingCole seeks to incorporate biophilic design and natural elements, whether with plants or daylight. As our buildings grow, we consider how to bring daylight into spaces for staff, patients and visitors. Additionally, using materials that reference nature can help reduce stress for everyone in the building.
Bisnow: What are some of the benefits to using modular and unitized construction for healthcare spaces?
Frazier: One of the goals of modular construction is to expedite build times. The concept is based on parallel processing. Foundations and exteriors can be built simultaneously, with bathroom pods that later can be installed quickly and easily.
Prefab also contributes to sustainability by reducing waste and lowering on-site environmental impact. By bringing in components, we minimize the need for cutting studs or drywall and disposing of materials on-site.
Another advantage is that we have a repeatable module and design. Modularity reduces the potential for small variations between teams that naturally arise from on-site work differences.
We're currently working on a project for the Hospital for Special Surgery’s Kellen Tower in New York City. The site is over FDR Drive and very tight, with essentially no lay-down space.
For this project, we are constructing large sections of the building off-site. The floor plate was designed in three components, which were transported up the river on a barge and craned over FDR Drive in three pieces. This required closing FDR Drive for three quick overnight operations to lift these components into place and then resuming construction afterwards.
Bisnow: What are some other healthcare projects that EwingCole worked on?
Frazier: We’re working with Northwell Health’s Center for Advanced Medicine on a modular project with an expedited delivery schedule. By partnering with Falkbuilt, a company specializing in prefab products, during the design phase, we were able to coordinate many details early that we might typically address during construction.
We're also designing many spaces to be flexible, allowing for an easy transition from administrative use to a clinic use with minimal changes.
For our other client, Geisinger Health in Danville, Pennsylvania, we're utilizing modular bathroom pods from Durapods. Due to a shortage of skilled labor in Danville, we turned to modular bathroom construction to address this issue and ensure consistent quality.
We began collaborating with Durapods early in the construction documentation phase to prepare the site for modular requirements, which differ from traditional stick-built construction.
For example, we must ensure a large enough opening in the building to allow each prefabricated bathroom to be craned in and placed within the hospital.
This article was produced in collaboration between Studio B and EwingCole. Bisnow news staff was not involved in the production of this content.
Studio B is Bisnow’s in-house content and design studio. To learn more about how Studio B can help your team, reach out to studio@bisnow.com.