Modular Construction To Be Used In High-Rise Housing In Oakland
Oakland will soon have the tallest prefab modular high-rise apartment complex in the country. RAD Urban is pushing forward with plans to build two 29-story high-rises with 200 units of housing using steel-framed modular units.
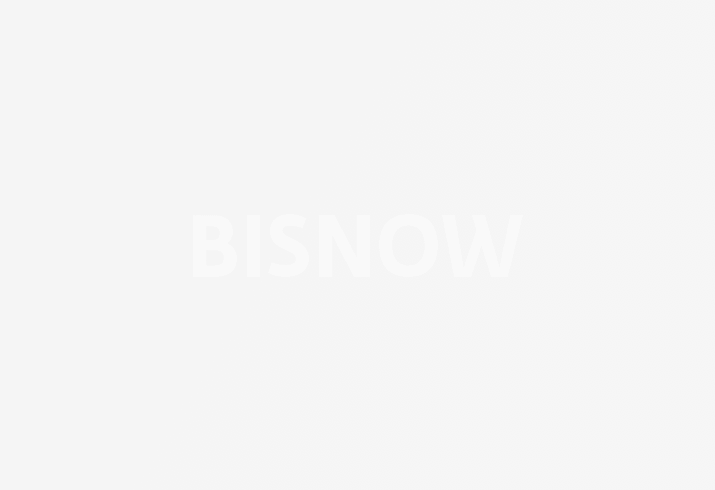
Unlike projects built with wood-framed modular units that top off at mid-rise level, projects built with steel-framed modular units can reach much higher, RAD Urban Senior Vice President, Construction and Operations Jason Laub said.
Modular isn’t new to construction and it has been around for decades, Laub said. Modular construction and other emerging construction technologies will be discussed at Bisnow’s upcoming Oakland Construction and Development Update! June 14.
The increased costs of construction has caused more people to look at modular as a solution and cost savings, Laub said.
“Developers are increasingly not able to make projects pencil,” he said. “We need to ... look for creative technologies to advance the industry and lower the cost to build and deliver housing."
Steel modular construction saves 20% on construction costs and time to completion compared to conventional stick-built construction.
Modular construction is quickly becoming an alternative to traditional construction to save time and money throughout the Bay Area.
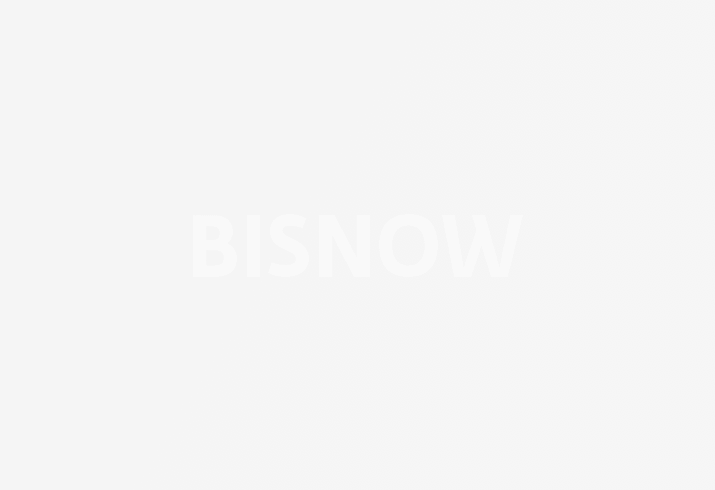
RAD Urban has built two modular projects in Berkeley and Oakland and has two under construction. The five-story Garden Village in Berkeley has 77 units and a rooftop farm. The building at 4801 Shattuck has 43 units. The under-construction project at 5110 Telegraph will have 204 units and a rooftop garden, while the project at 4700 Telegraph will have 48 units.
Several high-density modular products have been rising up in Oakland and Berkeley. Panoramic Interests has been building and planning additional modular housing. Its largest project will be a 1,000-plus-unit modular project in West Oakland. First Community Housing is building a five-story modular supportive housing project in San Jose with 135 units.
RAD Urban purchased a factory in 2013 to manufacture its own steel-framed modular units.
He said when the company looked into modular construction originally, the options available didn’t really provide a cost savings and were selling the times savings.
“Speed is good, but money is money,” he said.
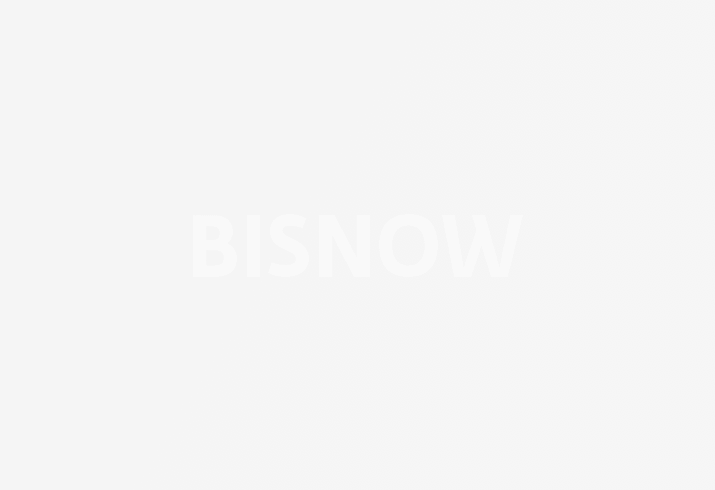
Laub said steel modular units have advantages over their wooden counterparts. Unlike wood-framed modular units, steel allows for high-rise construction.
Wood can still have issues with mold and often lower ceiling heights than steel construction.
Unlike wooden modular units that typically have five or six sides, RAD Urban’s steel units have four or five sides. Laub said the units are 90% to 95% completed with finishes and appliances installed. Its units are typically about 360 SF.
He said one of the challenges to building modular is that it means a lot more pre-planning. He said a lot of decisions about finishes have to be made early.
“This is just the reality of gaining the benefits modular has to offer,” he said.
RAD Urban has partnered with the carpenter’s union inside its factory. He said modular has received criticism from many unions in the past due to fear their jobs are being taken off the job site and moved into the factory.
Learn more about RAD Urban’s modular construction projects and other construction trends at Bisnow’s Oakland Construction and Development Update! June 14 at Scottish Rite Center.