Commercial Laundry Company Implements Sustainable Practices, Expands To New Philadelphia Facility
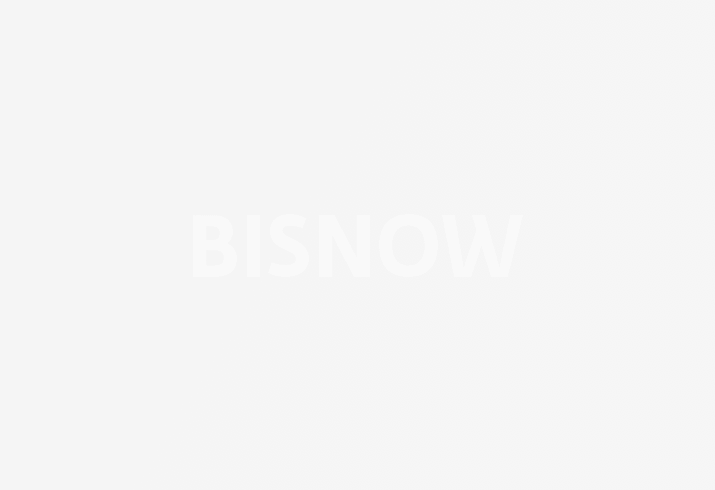
Arway Linen, one of Philadelphia’s largest commercial laundering services, has set its sights on two goals since 1979: efficiency and consistent growth.
Starting the business out of their apartment in the late 1970s, Arway founders Keith Harad and Hal Glestein scaled their company over several decades to a 30K SF facility in the Frankford section of Philadelphia, only to find years later that they had outgrown their space.
The company faced the difficult decision to either scale back operations or move to a new facility to continue its growth trajectory.
To the Arway team, which has now introduced a new generation of management, the answer was simple: grow and evolve to meet the industry’s heightened demand, especially considering the commercial linen supply and management industry is expected to grow 9.2% annually and reach a value of $107B by 2031.
“There was no room for us to be stagnant in our business,” Arway Linen Director of Operations Mark Harad-Oaks said. “The only true risk we faced was to not leap forward at all.”
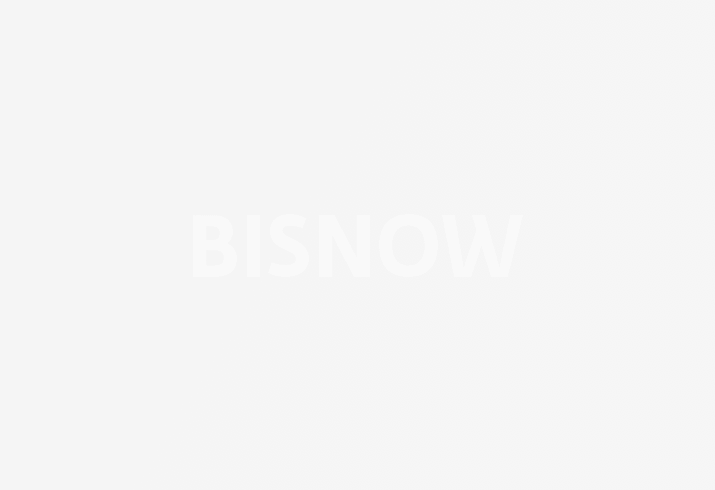
The team landed on a new facility in Philadelphia’s Port Richmond neighborhood. At 65K SF with a second 20K SF building and spread across 5 acres, it is a major upgrade from its Frankford facility.
Beyond more square footage, another vital requirement for the new building was that it could accommodate additional modern, energy-efficient laundry equipment as the industry evolves in favor of equipment that requires less energy to run and consumes less water, Harad-Oaks said.
“In our current facility, we were handcuffed regarding the type of equipment we could bring in because of the building layout, so to invest in modern equipment in this space was not feasible,” Arway Managing Partner Mario Stagliano said. “Any equipment that was brought in over time was either used or something you paid cash for, so there was really no financing for this business.”
The team started exploring more complex automation tools and modern laundry technology to see if it could be applied effectively in the new facility, Harad-Oaks said. It created a pro forma based on its weekly volume and discovered that new, energy-efficient equipment, though expensive, would pay for itself over time.
But the hefty upfront costs of this advanced machinery proved to be an obstacle for the company, Stagliano said. The team knew it had to get creative to find the best source of funding, or the project wouldn't pencil out as planned.
That’s where Ecosave, a provider of net-zero energy solutions, came into the picture.
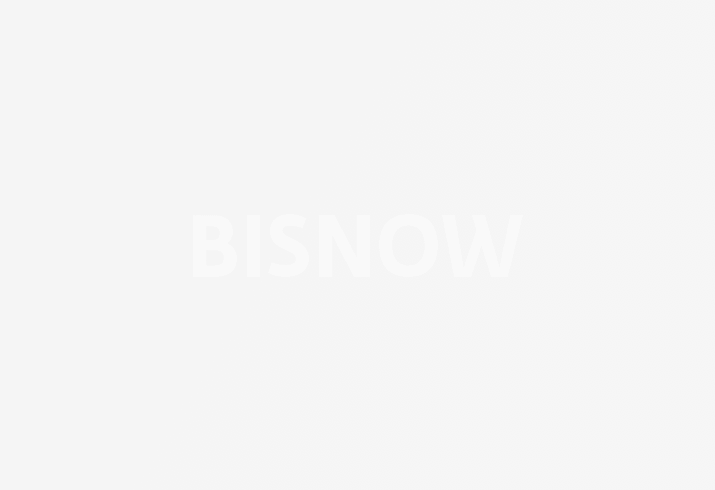
Ecosave’s engineering efficiency services partnered with Arway to customize the facility upgrades, accommodating the current and future needs of the firm. The upgrades include new equipment with industrial wastewater treatment technology that manages pollutants more effectively and artificial intelligence tools to better manage building systems.
“Ecosave is beyond proud to be partnering with Mario and the team at Arway as they expand operations in Philadelphia,” said Bretton DeNomme, chief operating officer at Ecosave. “Arway is a generational business with deep roots in Philadelphia and the surrounding communities it serves, and we are excited to see the company continue to grow with the assistance of our funding and engineering expertise.”
Other sustainability upgrades include solar panels affixed on the structure's roof, low-maintenance industrial dryers and ironers, and smart water valves that will significantly decrease water usage. These valves are designed to prevent backflow and ensure consistent water pressure throughout the building, Stagliano said.
“The new equipment will only use 0.7 gallons of water per pound of laundry, compared to the 3 gallons per pound our machines are using currently,” Harad-Oaks said. “This is a massive upgrade.”
The new facility upgrades are expected to reduce Arway’s total carbon impact and energy consumption by more than 50%, according to an analysis from Ecosave.
Ecosave invested about $20M in facility and equipment upgrades, including the funding of new laundry equipment. Due to less energy consumption, Arway will save an estimated $3M annually, which it is planning to reinvest to grow the business further, Stagliano said.
“It's very rare that a small business of our size can take on a project this big,” Stagliano said. “We’re proud to be a leader in our industry by spearheading sustainable practices.”
The new facility’s layout and design will allow Arway to expand and become one of the largest commercial laundry providers in the U.S., said Steve Curtis, sales director at Arway.
The company’s current facility can wash and produce about 200,000 pounds of laundry per week. The new building will allow for up to a million pounds of laundry to be washed and produced — five times its current ability.
Arway’s present capacity is also specific to food and beverage providers, like restaurants, caterers and country clubs, Curtis said. With the new facility, it can approach hotels and hospitals for their laundry needs as well as expand its geographical reach beyond the 60-mile radius it caters to now.
“We’ll be able to execute on everything we haven’t been able to in the past 15 years, and that’s an incredible achievement for our business,” Curtis said.
This article was produced in collaboration between Arway Linen and Studio B. Bisnow news staff was not involved in the production of this content.
Studio B is Bisnow’s in-house content and design studio. To learn more about how Studio B can help your team, reach out to studio@bisnow.com.