Getting It Built Faster: Why Projects Are Adopting Panelized Construction Methods
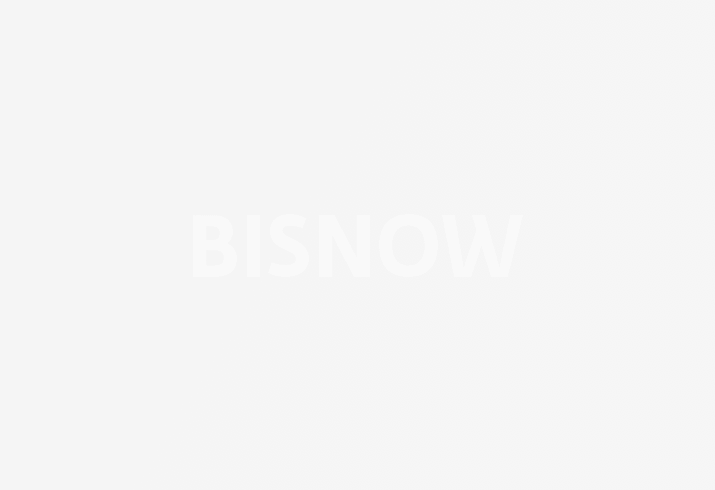
Traditional construction methods are time-consuming and labor-intensive, requiring the use of skilled tradespeople who are increasingly in short supply, said Jason Rhees, CEO of HercuTech, a manufacturer of panelized wall systems.
Conventional approaches have other downsides too. Volatile lumber and other material prices bring unpredictability to construction budgets. Conventional methods also generate waste while yielding an end product that isn’t particularly energy-efficient to operate.
That’s why Rhees said forward-thinking developers are experimenting with panelized construction, also known as prefab or off-site construction. This approach manufactures a building’s components in a factory and then assembles them on-site.
Panelized construction isn’t new, but the technology is evolving rapidly and gaining broader acceptance in certain types of construction, such as multifamily, Rhees said.
“The technology is gaining traction,” Rhees said. “More developers, as well as builders, architects and even municipal governments, are seeing it as an attractive and effective construction method. We’re getting more calls, and I hear from our peers and competitors that they are experiencing the same.”
One HercuTech client, Paragon Development Group, used the company’s HercuWalls panel system for the Hampton East build-to-rent, low-rise apartment community in Mesa, Arizona.
By using HercuWalls, Paragon completed its project two months faster than would have been typical with traditional methods, Rhees said.
“Paragon’s project was less exposed to fluctuating wood prices and required about half the man-hours to complete compared to traditional stick framing,” Rhees said. “Plus, because the panels provide airtight assembly, the community’s residents enjoy up to 40% lower energy costs than with traditional construction.”
HercuWall panels are made of expanded polystyrene foam, or EPS, that is reinforced with steel in a proprietary method patented by HercuTech, and laminated with a weather-resistant barrier. They are three times stronger than traditional wood framing, yet panels are light enough to be carried by one installer, Rhees said.
In addition, HercuTech’s panels provide thermal and sound insulation when used as interior demising walls.
“This creates an excellent sound barrier, which means Paragon could increase both the density of the units in its Hampton East community and expand the community’s open spaces, making the project more appealing to prospective residents,” Rhees said.
‘High Degree Of Quality Control’
HercuTech uses proprietary software to convert architectural plans into precise shop drawings. This ensures accurate panel fabrication, simplifies on-site installation and reduces the risk of cost overruns, Rhees said.
“Because HercuTech wall panels are manufactured in a controlled factory environment, we can ensure a high degree of quality control,” Rhees said. “We take our clients’ plans and design everything in the 3D-modeling program Revit.”
As panels are fabricated, they are numbered in the order in which they will be installed on the building slab, Rhees added.
The result? A system that requires minimal training and no carpentry experience to implement, he said. Other benefits include faster construction, less need for excess materials and a reduction in on-site errors.
“The panels are lightweight and designed for easy handling, allowing for quick assembly with minimal labor,” Rhees said.
Speed Of Assembly
Rhees said the speed and efficiency of panelized construction can be hard to envision for someone who is used to traditional construction approaches.
“However, thanks to all the prework, the building stands up extremely quickly,” he said.
Laborers can install one housing unit’s worth of panels in 45 minutes. The building envelope is then completed through the process of filling voids in the panels to create a concrete stud wall. This takes another 45 minutes.
“Once the exterior and interior wall systems are installed, the other building trades can easily follow up to do their work,” he added.
In the case of Hampton East, HercuTech’s preconstruction process ensured the efficient integration of electrical, plumbing and HVAC systems, minimizing on-site errors and delays.
At the macro level, Rhees said panelized construction’s reduced build times and streamlined processes could help address the housing shortage the U.S. is grappling with.
“By speeding things up and cutting costs, we’re making homes more affordable for people,” Rhees said. “These days, delivering quality housing to more communities that need it — faster and at scale — is something this country desperately needs.”
3-In-1 System
Another advantage to HercuWall panels is that they create an airtight building envelope, reducing air leakage and energy consumption.
“The system incorporates insulating foam and galvanized steel, which contribute to better thermal performance and lower energy consumption,” Rhees said.
Together, the insulation, steel and weather-resistant barrier, HercuTech’s 3-in-1 system, provide superior durability, including resistance to extreme weather conditions, pests and mold, Rhees said.
“The resulting buildings are low-maintenance structures that are built to last,” Rhees said. “It’s also a climate-resistant product.”
As a bonus, general liability insurance premiums tend to be lower for HercuTech homes, as insurance companies recognize the superiority of its concrete steel EPS system to wood construction, Rhees said.
While HercuTech’s panels are most widely used in single-family residential construction, the technology is gaining traction in other sectors, including multifamily housing and commercial buildings, Rhees said.
“We can go up to five stories on top of each other,” Rhees said. “HercuTech walls can be used as a window wall, but also a curtain wall, with different components.”
Advantages For Architects
Unlike competing modular construction solutions, HercuTech’s wall panels are made “per plate height,” meaning architects don’t need to conform to a manufacturer’s standard size, Rhees said.
Fabricating panels to exact heights while including openings for windows and doors reduces time-consuming, costly on-site modifications.
“We offer panels in various heights, which allows for more customized and precise construction and ensures each project meets specific design criteria,” Rhees said, adding that his company’s panelized wall system is earning industry awards.
Paragon’s Hampton East project, described as combining “luxury living with a contemporary architectural style,” won the Arizona Multihousing Association’s Developer’s Award for Best Community Design.
“The technology creates a better experience for residents,” Rhees said.
Still, what attracts developer clients is the system’s predictability in pricing, sourcing, quality and labor requirements that mitigate risks and streamline the construction process, Rhees said.
“Looking at the pro forma of the projects, it becomes evident they are much more lucrative when using this type of technology,” Rhees said. “Our repeatable plans drive efficiency, which is what our developer clients recognize us for. These are builders that want to build better and recognize they can do so by leveraging this new way of doing things.”
This article was produced in collaboration between HercuTech Inc. and Studio B. Bisnow news staff was not involved in the production of this content.
Studio B is Bisnow’s in-house content and design studio. To learn more about how Studio B can help your team, reach out to studio@bisnow.com.