Scalability, Standardization Stand In The Way Of Bay Area Builders' Use Of Modular, Mass Timber
The inability of modular housing manufacturers to create economies of scale, hurdles to financing and regulatory challenges make it difficult to develop sustainable affordable housing in the Bay Area.
Although modular construction has been around since ancient Roman times, in recent years it has emerged as a popular approach to solving California’s housing crisis. When perfectly executed, developers can build projects faster and at a fraction of the cost of conventional construction projects.
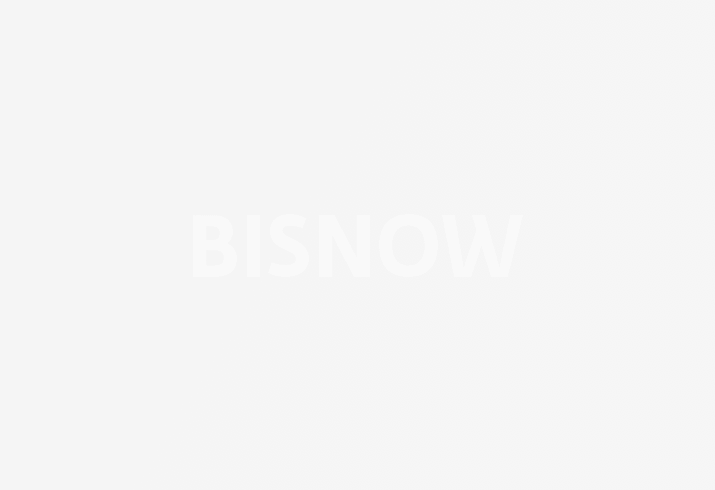
But cost savings and timeliness are evading modular builders, partially due to market forces like high interest rates and supply chain slowdowns, panelists said at Bisnow’s Bay Area Prefab, Modular and Mass Timber Conference July 30 at the Grand Hyatt in San Francisco.
“Ninety-nine percent of all projects that are permanent modular construction are 100% custom-engineered prototypes from the ground up,” Synergy Inc. CEO Justin Stewart said. “We all see the benefit of optimizing a living unit and repeating it. It's just not there yet.”
The lack of uniform guidelines and the proliferation of customized components elevate prefab construction costs, R2 Building founder Randy Miller said.
“An unacceptably high percentage of projects experience severe weather damage, trade damage and drywall cracking,” Miller said. “We have to focus on the idea of standardization. It can really bring costs down.”
The industry’s inability to scale has led to inefficiencies, AMJ Construction Management Director Brian Caruso said.
“When we think of modular, it's almost like Legos that we used to play with as kids,” Dignity Moves co-founder and Chief Real Estate Officer JoAnne Price said. “Why can't we just do that with rental units? We're trying to merge two industries, the manufacturing industry with the traditional construction industry, and there needs to be alignment. It's not rocket science, so why can't we solve it?”
Shorter construction times mean the unhoused can get off the street faster. But delays on factory floors result in delayed deliveries of much-needed affordable housing, Price said.
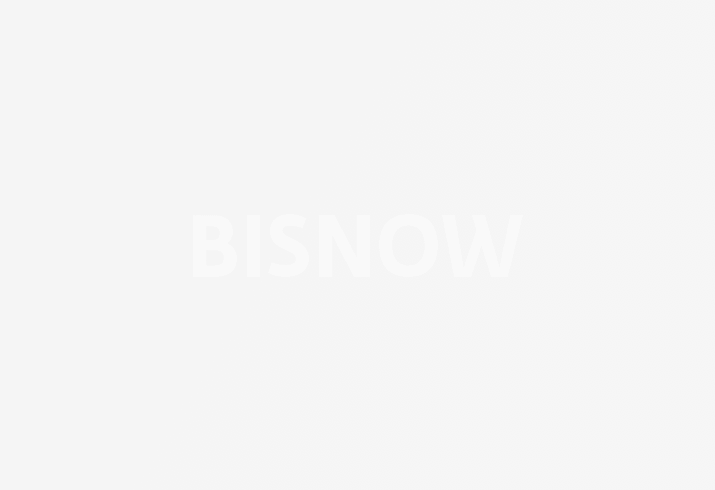
“I've seen modular delays as much as a month and even six weeks,” she said.
For Dignity, timeliness is critical since the organization provides interim housing for families in as little as four months.
A strong general contracting partner will help developers avoid lengthy delays, Price said.
“You should select partners who are going to be with you from the get-go,” she said. “And when I look at our key partners, it's been Gensler and Swinerton Construction, because I can't emphasize the amount of pressure that's on the teams to deliver.
“When things go wrong with the modular vendor, which they typically do, your GC can turn this around for you.”
The mission of all parties involved in construction should also align, panelists said.
“We're delivering completed projects that people can live in. So when you integrate on the front end, thinking about it from that perspective, the team members become very clear,” Stewart said.
Stewart cited an affordable housing project Synergy built in Seattle.
“We lost our modular supplier a month before they were going to start,” he said. “We had to switch modular suppliers one month before startup model production. And we were able to transition the drawings. So, the project owned all of the materials, we were able to switch manufacturers and deliver it with a slight cost savings.”
Financing hurdles further complicate the delivery and production of sustainable modular and mass timber affordable housing.
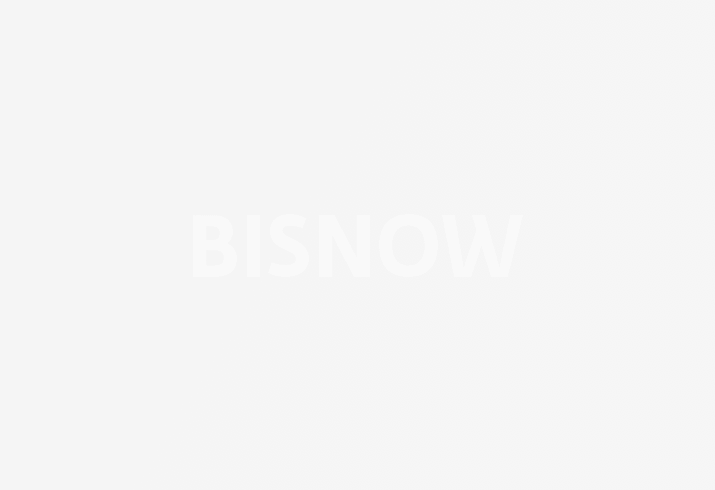
Hayward-based nonprofit developer Eden Housing deals with the stress of applying for and securing low-income housing tax credits and often onerous local and state zoning laws.
“We are required to have perfect payment and performance bonds on all of our deals because of the various money that we get from different agencies,” Eden Chief of Real Estate Development Andrea Osgood said. “But many of the builders that do modular don't provide them. So that becomes a challenge.”
If Eden can’t locate bridge financing, it often has to pay 30% of the modular company’s contract upfront, Osgood said.
Synergy recently started an eight-story, market-rate student housing project in Berkeley where each floor was “perfectly” constructed at a great cost point, Stewart said. The general contractor had to provide a bridge loan to cover a financing gap it incurred. In fact, he said this has become a new trend among general contractors in recent years, even though they are far from being financing experts.
Despite the hurdles facing the affordable housing industry, some mass timber and modular builders are scaling, resulting in cost and time savings.
Oakland-based oWow Development has developed two notable mass timber projects in an urban area with high barriers to development, downtown Oakland.
The company’s first project at 316 12th St. in Uptown Oakland was a five-story property with 27 apartments and commercial space, oWow CEO Danny Haber said.
“This project hit $280 a foot hard cost and exceeded our schedule,” Haber said.
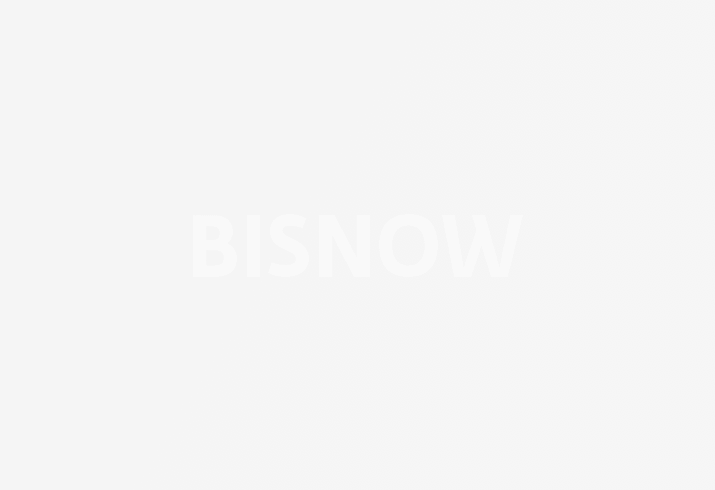
At 1510 Webster St. in Oakland, oWow is building the tallest mass timber building on the West Coast.
“It was a 65-day experience from pour to close,” he said.
Panelists were generally optimistic about the future of sustainable mass timber development — if the industry moves toward scaling.
“Modular should be here to stay,” Price said. “We should be making it work to address our housing crisis.”