5 Reasons To Use Off-Site Construction
The construction industry is one of the largest industries in the world, with around $10 trillion spent on construction-related goods and services each year. But what is holding back the complete transformation of the construction industry? Despite the availability of advanced technology, processes and innovation, construction continues to fall behind other sectors in productivity.
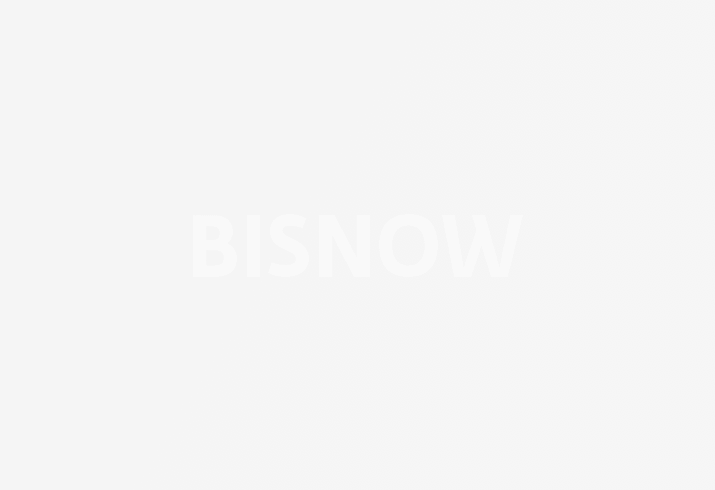
Labor shortages, scheduling, high costs, quality concerns and safety all impact the industry’s ability to increase productivity, but the movement toward off-site construction and prefabricated systems can alleviate many of those pains.
Here are the top five reasons to consider prefabrication.
1. Shortens schedules.
Off-site construction can deliver a project 30% to 50% faster than traditional methods because building construction occurs simultaneously with the site and foundation work. Schedule delays due to weather and other external factors are a non-issue given that the build takes place in a controlled environment. In a McGraw Hill survey, 72% of contractors said the use of prefabrication decreased project schedules by more than a week, and 37% said it reduced the schedule by four weeks or more.
2. Reduces site impacts
Off-site construction translates to fewer workers and less equipment littering the building site, reduces traffic, requires fewer staging areas and increases job-site safety. The result is a significant reduction in pollution and noise, allowing for an accelerated construction timeline while maintaining high standards of quality.
3. Delivers early cost certainty
By engaging in the design process early, the project’s design team and other key players align on project requirements from the beginning. This collaboration and transparency gives all parties visibility into factors affecting the bottom line of the project’s budget.
4. Reduces waste
When comparing construction to manufacturing, 57% of activities in construction are wasteful and do not add value, according to the U.S. Bureau of Labor Statistics. In manufacturing, 62% of activities add value. Replacing the wasteful elements of construction with manufacturing benefits through off-site construction can remove waste and increase value for projects.
5. Saves on labor costs and solves problems related to the skilled labor shortage
With a labor shortage, prefabrication enables work to be done by fewer, highly skilled workers. Off-site construction allows skilled craftsmen a safer and more productive place to do their job and quality can be monitored throughout the production process.
To learn more about Bisnow content partner Clark Pacific, click here.