A Turnkey Approach Fits Parking Into Tight Spaces
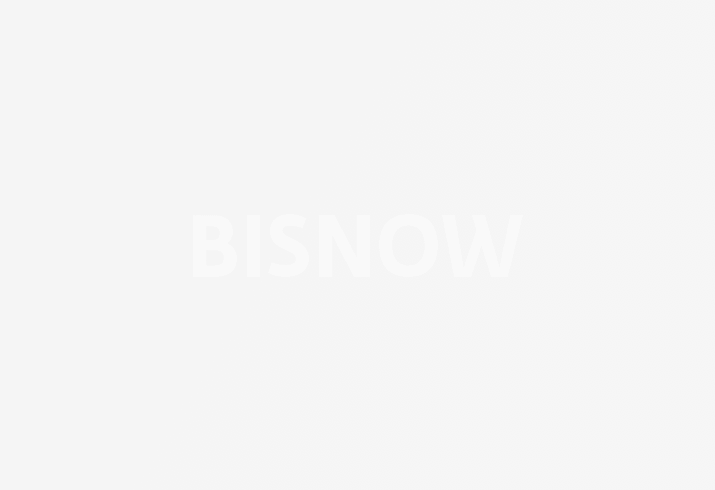
Most people take parking garages for granted. They expect them when they arrive at the office or the mall and don’t think about them again after they park their car. Parking structures fulfill the task of fitting many spaces onto a small footprint, making life easier for tenants, guests and nearby businesses.
Despite their ubiquity, construction of these structures can prove to be difficult, especially with the challenge of fitting a several-story-tall concrete building onto a tight construction site hemmed in by neighboring structures and busy roads — without causing logistical or safety problems.
“Putting up a new building is messy,” said Mahil Keval, product manager for PARC, the parking structure arm of prefabrication specialist Clark Pacific. “If you're an owner, there is a lot you’ve got to think about, like ‘Who am I going to get to design this?’ and ‘Who am I going to get to build this?’ Plus, there are so many different phases and components involved in a construction project.”
Such was the dilemma in the construction of three new parking deck structures for the Coleman Highline mixed-use development in California, the most recent of which was completed in October. The site straddles the San Jose-Santa Clara border, but the challenges it presented were more substantial than mere lines on a map.
Rather than being conveniently located in a large vacant field with plenty of workroom, the three structures would share space with at least eight other buildings, including hotels, retail, 1,600 apartments, a Major League Soccer stadium and a nearby practice field. The 1.5M SF development is a hub of activity, and the challenge was to build 4,275 parking slots — with another 1,136 planned in a fourth building — without disrupting or endangering the tenants and residents.
Project owner Hunter Properties decided that a conventional approach, which could span multiple years and involve multiple work crews and hundreds of people on-site each day, was not practical.
Other concerns included the project budget and timeline. Keval explained that Clark Pacific addressed those concerns for Hunter Properties with a turnkey approach in which it designed, engineered, manufactured and installed the new buildings itself. The majority of the work was performed off-site at one of its three precast concrete manufacturing plants in the state, allowing one building to wrap construction in just nine months.
“We literally take the ‘messy’ off-site so that, ultimately, we're manufacturing and delivering a set of prefabricated components directly to the site,” said Mickey Ankhelyi, PARC director of architecture. “And there's not a lot of people out there on the job site because most of the work was done in the plant.”
Not surprisingly for a Northern California project, built-in infrastructure for electric vehicles was a priority for owner Hunter Properties. The newest and largest of the structures — standing five stories tall and spanning approximately 655K SF — includes charging stations for 130 EVs.
A rule of thumb for new parking structures is to dedicate 6% of slots to EV charging, Ankhelyi said, although clients or local jurisdictions might call for more. That is on top of the many other features that can be added inside and outside of the basic structure to customize it to the client’s needs.
He said Clark Pacific has manufactured parking facilities that range from bare-bones structures to amenity-rich garages for Class-A office buildings that might include a car wash/detailing station, dry cleaning drop-off and restrooms. Increasingly, these spaces aren't just for motorized vehicles but include ample space for bicycle storage.
“We have one client where each of their parking structures has an amenity on the rooftop,” Ankhelyi said. “The very top floor of one is an athletic field with showers and locker rooms.”
Such amenities, he said, are easily incorporated into prefabricated parking structures. Exteriors, too, can be designed and installed to fit seamlessly with the look of the surrounding campus. For instance, one of the Coleman Highline buildings features exterior Corten steel accents to complement the office building it serves.
“Our parking structures essentially start as a pre-engineered chassis and what the exterior skin is, at the end of the day, can be anything,” Ankhelyi said. “You can do all sorts of things on the outside. But at the core, it is a pure rectangle, and it's a very efficient design.”
The design-build approach, Keval noted, works best when there is close coordination between the client and the Clark Pacific team throughout the process, as was the case for the Coleman Highline buildings.
“We do our best work when we have control over all the variables, and the ideal scenario is where the owner is contracting with us directly and early,” Keval said. “When you rank our delivery versus a traditional design-build delivery from a cast-in-place competitor, we can be cost-competitive with those guys while delivering higher quality and a faster, more efficient garage. But the linchpin to it is that we need early involvement from the client, and we need them to make decisions early as well.”
This article was produced in collaboration between Studio B and Clark Pacific. Bisnow news staff was not involved in the production of this content.
Studio B is Bisnow’s in-house content and design studio. To learn more about how Studio B can help your team, reach out to studio@bisnow.com.