Bringing 3 Bay Area Multifamily Developments To Life With Metal Framing
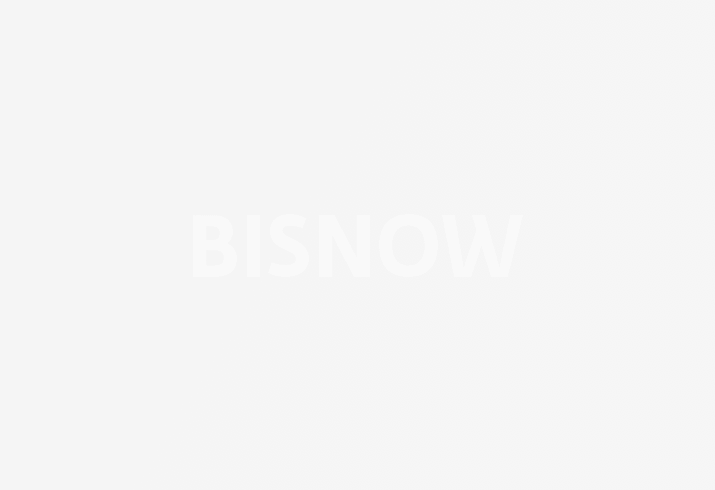
A multifamily complex next to Oakland’s biggest transit station. High-end condominiums overlooking the bay from Yerba Buena Island. Housing for a high school faculty and staff in Daly City. Though they are scattered across the Bay Area and though their exteriors are markedly different, each of these housing developments was brought to life with the same design philosophy and material: metal framing.
Structural light gauge steel framing is an alternative to wood-framing construction that can allow housing to be built more reliably and often more affordably than with concrete or wood. Most commonly used for mid-rise multifamily buildings, metal-frame construction is becoming more popular, thanks to a spike in lumber costs.
Developers looking for cost-effective ways to meet the need for denser housing in U.S. cities have been experimenting with metal framing. But while most contractors and owners are new to light gauge steel, a select few have been framing with metal for decades and have refined their techniques to maximize efficiency and design.
Anning-Johnson Co., a national specialty contractor with decades of structural metal framing experience, has worked to become the industry leader in metal-framed structures, particularly through its collaborative design-build approach.
“Every single piece of the structure is optimized to create efficiency and minimize waste,” Anning-Johnson Chief Estimator Mitch Hookins said. “We pre-cut and bundle all the framing members per unit and crane them into place for just-in-time delivery. There’s 20 years of value engineering built into our process.”
Having seen every imaginable job site challenge with light gauge steel, Hookins said Anning-Johnson has metal framing down to a science. Read on to learn more about the many possibilities of metal framing.
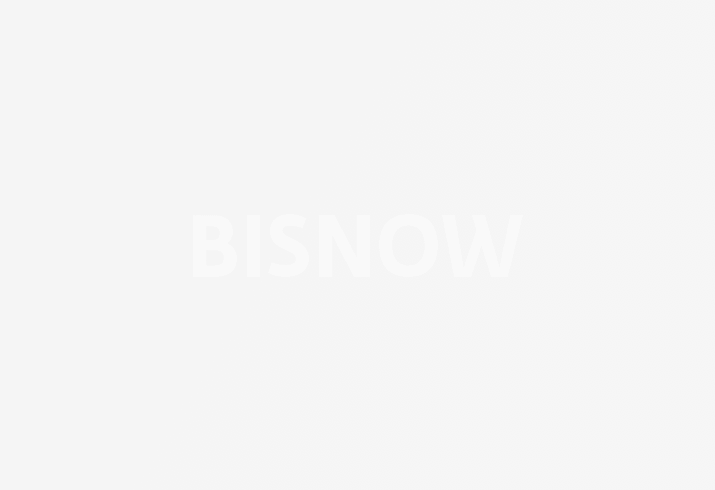
MacArthur Commons, Oakland
MacArthur Commons, a three-building, 325K SF multifamily complex next to the BART system’s largest station, was intended to be built with modular wood-framed units. But after a change in ownership, a new general contractor called in Anning-Johnson to rethink the design.
The firm’s design-build experience allowed Anning-Johnson's team to quickly determine a fixed price to redesign the buildings’ 378 units with light gauge metal. In eight weeks, the designers had a fully rendered plan for the new buildings. Construction from the podium slab to roof was completed in only nine months. The project made up the lost time and delivered on schedule, thanks to the time-efficient and cost-effective solution offered by light gauge metal.
The ability to lock in metal prices can give owners peace of mind, unlike wood prices, which fluctuate along with the cost of lumber. With more wood-framed multifamily buildings in the Bay Area becoming the targets of arson, owners can also feel secure that their construction sites are noncombustible. That safety often brings the added benefit of lower insurance payments.
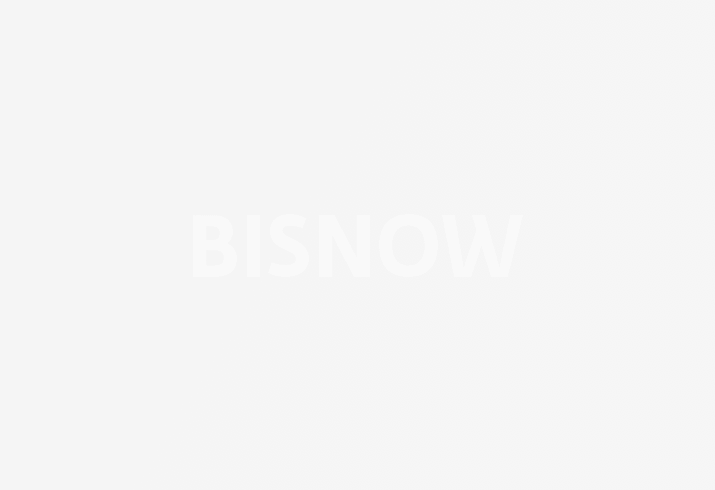
The Bristol, Yerba Buena Island
The construction of the Bristol condominiums is part of the widescale redevelopment of Yerba Buena Island, best known as the piece of land that connects the east and west spans of the Bay Bridge. While The Bristol’s developer had considered other structural systems, Anning-Johnson’s proposal proved a more attractive financial option.
“Most light gauge steel projects involve repetitive stacking structures over a single concrete podium, but the irregular shapes and junctions of the Bristol’s units, designed to give each one a distinct layout and view, made the project considerably more intricate than most,” Anning-Johnson project manager Robert Hansen said.
Hansen’s team worked with the designers and architects to include oversized picture windows that would take advantage of the commanding views of the San Francisco Bay.
To contend with the building’s complicated architecture, Anning-Johnson and its design-build engineer produced a full structural BIM model. This allowed them to partner with the general contractor in a full BIM coordination effort for every piece of the 175K SF structure, from the multi-tiered concrete podium and the central courtyard to the 124 units above.
“This was an especially complex job, so we leaned heavily on our prior experience to find creative solutions for unique and difficult conditions,” Hansen said. “Most often it was our team in the field proactively suggesting solutions to the structural engineer. This allowed us to continue pressing forward, rather than losing time waiting on answers, so we could turn over a seven-month project duration on schedule.”
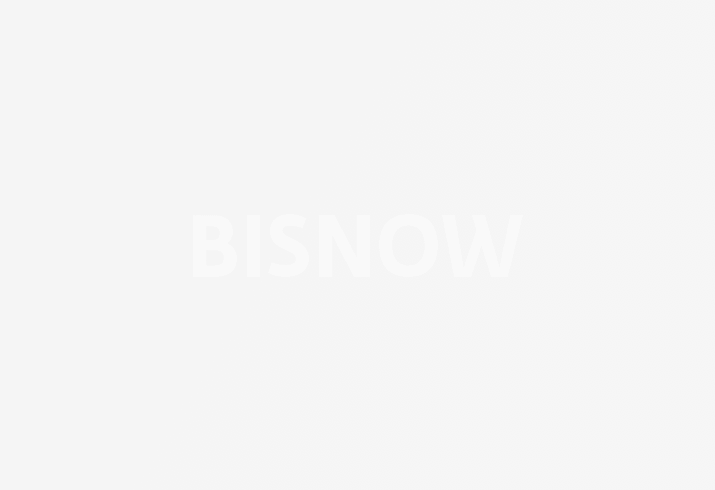
Serramonte Del Rey Faculty & Staff Housing, Daly City
In 2019, the Jefferson Union High School District issued a design competition to build a complex of subsidized housing for its faculty and staff in Daly City. Having seen Anning-Johnson’s work on MacArthur Commons from the highway, a general contractor proposed to Hookins that they collaborate on an entry. The 122-unit, 144K SF light gauge steel design won the competition, and construction is now nearing completion at the site.
“This project has been especially collaborative, as the GC, architects, Anning-Johnson and the other major design-build trades were all on the same team from the very beginning,” Hookins said. “When you choose metal framing from the start, without the headache of initially designing with wood or concrete, you can save a great deal of time and money.”
This article was produced in collaboration between Anning-Johnson and Studio B. Bisnow news staff was not involved in the production of this content.
Studio B is Bisnow’s in-house content and design studio. To learn more about how Studio B can help your team, reach out to studio@bisnow.com.