Off-Site Building Is 'Ripe' For AI. But Are These The Robots You're Looking For?
If a lack of innovation is to blame for stagnating U.S. construction productivity over the last half-century, off-site builders — and some of their AI partners — think they may have the solution.
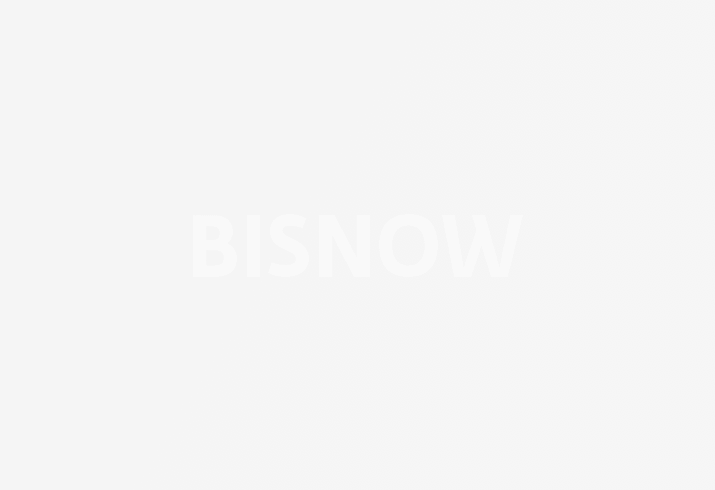
Around the country, prefabrication companies of different scopes and specializations are trying to boost their factory environments by using artificial intelligence.
Off-site construction firms promise both time and cost savings, with one June report by McKinsey predicting up to 50% quicker builds compared to on-site construction. Cost savings from off-site construction, on the other hand, only now appear to be materializing for builders, in part because of the use of AI.
Prefab construction in general is poised to take off in the next decade, especially in markets plagued with shortages of labor and housing like the West Coast of the U.S. and the United Kingdom, or for highly standardized property types like affordable housing, student housing and hotels. By 2030, modular construction alone could account for a combined $130B of new real estate construction in the U.S. and Europe and lead to $22B in annual cost savings, according to McKinsey.
Finding smarter, cheaper, faster ways to build those much-needed projects has tech firms (and their attendant financiers) taking notice, and venture capitalists haven’t been shy about throwing money at some of the bigger off-site construction companies. Menlo Park prefab startup Katerra’s most recent round of funding from SoftBank put its valuation up to $4B. Nearby off-site builder Factory OS is also expanding after new financing.
Other companies are building their own AI systems. North Carolina-based modular construction company Prescient has its own proprietary artificial intelligence technology and a $650M valuation.
“Every building that we produce and erect, we're gathering that [AI] data to drive the execution throughout the different processes, from design, engineering and manufacturing,” Prescient CEO Magued Eldaief said.
Prescient builds up to 17-story multifamily buildings with its prefabricated light-gauge steel structure system. To date, the company says it has worked on 40 buildings across 15 states in the U.S., including the 17-story, 336-unit apartment tower called Generation Atlanta in the Georgia capital's downtown.
Through its factories in North Carolina and Colorado, Prescient has collected a plethora of data that its AI uses to sequence logistics and assemble the building, according to Eldaief. That process has led to Prescient embarking on what will be the largest student housing project in the U.S.: The Green at West Village at the University of California, Davis.
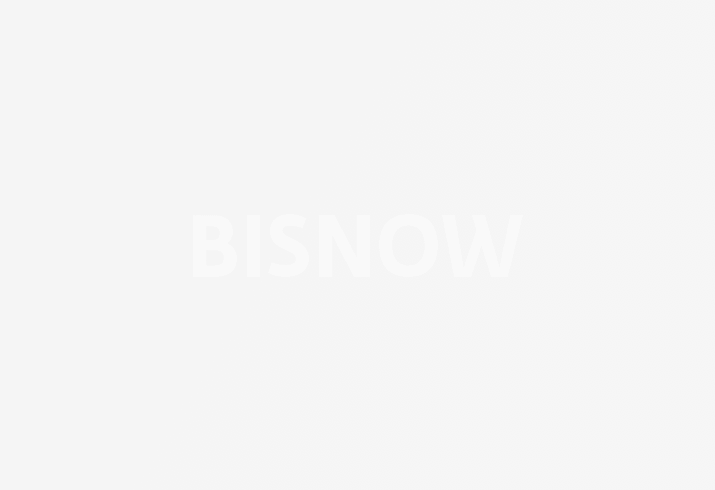
In another part of the sector, Arizona-based Kapture Prefab partnered with construction intelligence startup Indus.ai earlier this year.
Kapture makes interior and exterior building panels and was introduced to Indus through Sundt Construction, which has been using the California company’s computer vision technology for on-site construction.
The San Francisco tech company sets fixed cameras around job sites, and its AI translates the footage into data metrics that describe things like the movement of materials and labor deployment at various areas of the site.
On a whim, Kapture CEO Jason Anderson said, his company decided to give Indus.ai a try in its Tempe factory. So far, neither company has looked back.
“Once they came to our factory, I think they had an 'a-ha moment' and thought they had been attacking the wrong environment,” Anderson said. “This environment is ripe for AI because it’s controlled and easy to collect data.”
Several companies provide a similar construction intelligence through AI that Indus.ai does, but at least most are for on-site construction or other industries.
OpenSpace is a Bay Area company that uses machine and computer vision via 360-degree cameras to generate a visual of a job site and facilitate greater coordination among trades. In less than two years, it has collected 100M SF of data – or “six Empire State Buildings a month of data,” according to CEO Jeevan Kalanithi – that the company will use to provide future construction crews even more intelligence.
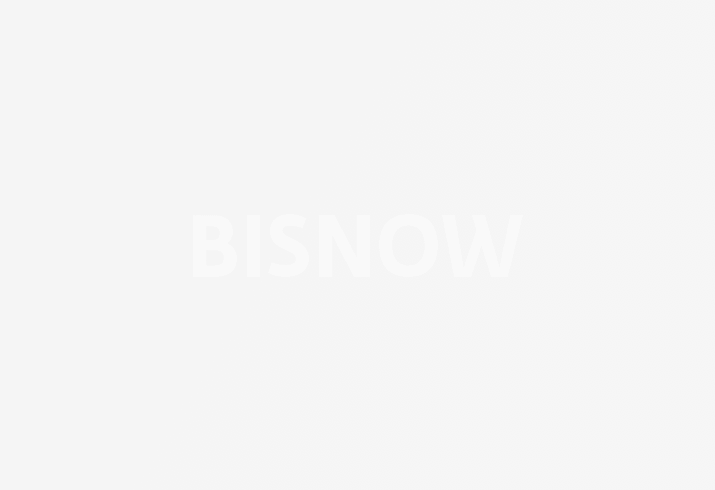
“We want to not just organize all the images, but to start analyzing what’s in them, so users can find exactly what they want even faster than [they can] today,” Kalanithi said. “It will be tracking things that are important for getting a job done on time."
There are several other camera-based construction intelligence companies like Indus.ai and OpenSpace, including S.F.-based Multivista and HoloBuilder. A few industry-unspecific manufacturing intelligence startups, like Bright Machines and Tulip Interfaces, have attracted tens of millions of dollars in funding.
But Kalanithi couldn’t think of a company focused solely on prefab construction, even though he sees a clear fit. Ryan Ware said his interior prefab construction company, Vantis, was in talks with Indus.ai because of its applicability to the factory environment.
“Off-site becomes even more of an opportunity to mitigate some of the challenges we have with projects like labor shortages, cost overruns and safety,” Ware said.
FullStack Modular CEO Roger Krulak said the company uses artificial intelligence in its current workflow and will likely partner with a set of companies, including Nikon and SiteAware, to expand its AI capabilities. FullStack made the tallest modular building in the country in the 32-story Brooklyn project at 461 Dean St.
"We use some optimization processes in a finite scheduling process, which is definitely machine learning and intelligence," he said. "You learn how efficient you are or if there's a bottleneck."
Sto Corp. CEO David Boivin's firm supplies the Sto Panel Technology network with much of its building material. A manufacturing expert who has led the production of goods from dishwashers to rechargeable batteries, Boivin is optimistic about computer vision AI’s value for all industries, but especially off-site construction.
In Sto Panel Technology’s case, the network is combining its new AI capability with production layouts designed by Porsche Consulting Inc., which design for minimized worker movement from the line through optimal material placement, among other adjustments.
“I think it’s brilliant,” Boivin said. “From what we’ve seen so far, by combining the cameras with what Porsche is doing, 200%, 300% or even 400% kind of improvement is possible in our operations, which is crazy but can be done.”
For a construction industry still stuck at 1960s productivity levels, crazy might just be worth a try.
CORRECTION, AUG. 7, 5:21 P.M. PT: An earlier version of this story misattributed a quote by Magued Eldaief to Mariel Ebrahimi and incorrectly implied Prescient's $650M valuation was due to its proprietary artificial intelligence. Eldaief said its AI makes it more productive, not more valuable. His comments have been updated.