How Precast Concrete Reduces Data Center Construction Costs While Accelerating Schedules, Meeting Green Goals
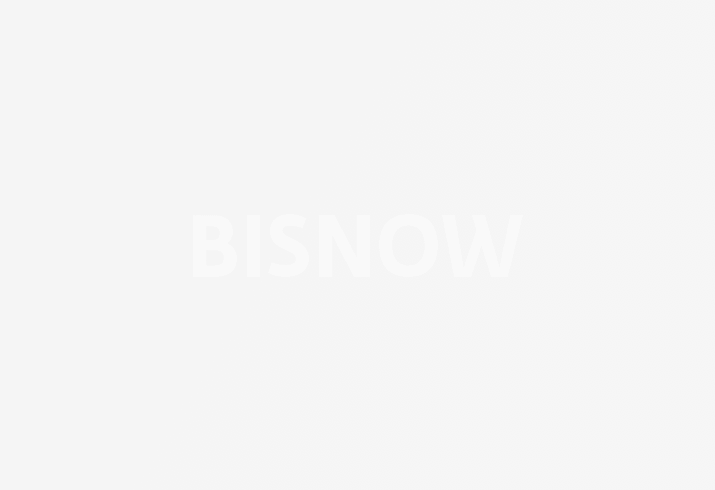
With data center demand projected to rise 10% each year until 2030, more flexible and resilient build-outs are becoming increasingly important to compete in this fast-evolving industry.
One option to help keep up with demand is precast concrete, which expedites the construction process by fabricating the structure and enclosure off-site. Precast concrete also helps maximize space, keeps data centers running at more manageable temperatures and reduces their carbon footprint, a problem that plagues facilities today.
Manufacturers of prefabricated building manufacturing systems like Clark Pacific are refining precast techniques to allow data centers to be built faster while reducing costs and environmental impacts.
“We’re not only working on streamlining building techniques but transforming our prefabrication materials to reduce carbon emissions,” Clark Pacific Chief Sustainability Officer Allan Bedwell said. “We’re able to erect data center structures 30% to 50% faster than the competition, which shaves off two to four months of build time while saving tens of millions of dollars for a typical 100-megawatt data center.”
Bedwell said Clark Pacific's prefab engineering and manufacturing team prioritizes customization before the building process begins. This is helpful if a data center owner expects they will need to transform or expand the building in the future, without implementing expensive scope changes that come with performing retrofits on-site.
“What we're seeing is a need to ensure the design maximizes space and superimposed load capacity for the servers and cooling systems,” he said. “Those two aspects are rapidly evolving in the data center space.”
All of these considerations are critical to building more efficiently and increasing a data center owner’s revenue, he said.
Data centers are responsible for nearly 1% of energy-related greenhouse gas emissions, and reducing this number has become a top priority. Data centers also consume large amounts of energy, and as the world transitions to green power, owners increasingly are turning their focus to embodied carbon. Clark Pacific is helping to answer the call using its CarbonShield product.
CarbonShield is a reduced carbon concrete mix that is not only durable but helps ramp up production for greener data centers while ensuring their high performance and longevity.
Bedwell said Clark Pacific’s years of precast concrete experience and engineering expertise can accommodate each client’s specific needs while prioritizing structural integrity, energy efficiency and faster build times.
As access to data becomes more valuable, Bedwell said that having a sound structural design is integral to project success.
“Our structural design has become increasingly large in scale to meet client needs, such as a 60-foot by 42-foot structural grid system supporting 600 pounds per square foot,” Bedwell said. “The pounds per square foot loading is dramatically increasing as servers become heavier with denser computing power and the weight of liquid cooling to optimize these processes.”
Clark Pacific recently worked with a client to deliver a large data center four months faster than traditional construction by manufacturing its structure and exterior off-site. In addition, the use of CarbonShield in the precast manufacturing process benefited the local community by reducing Scope 3 emissions.
Clark Pacific Senior Product Manager Jon Mohle said he likes to think of this approach as a “configurable” solution that uses a standard kit of parts to accommodate a client’s unique needs.
“This is one of the advantages of prefab where we have a select number of shapes that are configurable to different systems,” Mohle said. “The trick is not only thinking of customization in the beginning but how to balance the flexibility needed, which can give our clients a quicker turnaround in the delivery schedule.”
Mohle said precast concrete can also help data centers accommodate larger design loads as equipment density and weight increase to meet today’s data processing needs.
“We are seeing design loads rapidly increase from 250 pounds per square foot two years ago to nearly 600 pounds per square foot on work we are currently bidding,” he said.
Data center operations are also becoming hotter, which is why Clark Pacific plans to continue to innovate its precast systems to accommodate liquid cooling systems.
The long-term goal for Clark Pacific is to create a standardized product that has net-zero embodied carbon in addition to continuing to lower time to market and reduce costs, Bedwell said.
“We welcome the challenge from different owners and operators to think of creative solutions to future-proof these sites with better environmental and structural designs,” Bedwell said. “We want our product to be integral with the ever-changing needs of data center construction.”
This article was produced in collaboration between Clark Pacific and Studio B. Bisnow news staff was not involved in the production of this content.
Studio B is Bisnow’s in-house content and design studio. To learn more about how Studio B can help your team, reach out to studio@bisnow.com.