Labs Of The Future: The Design Trends Impacting Bay Area Life Sciences
From adding more traditional office design to incorporating wellness, research and development space in the Bay Area is setting a standard within the life science industry.
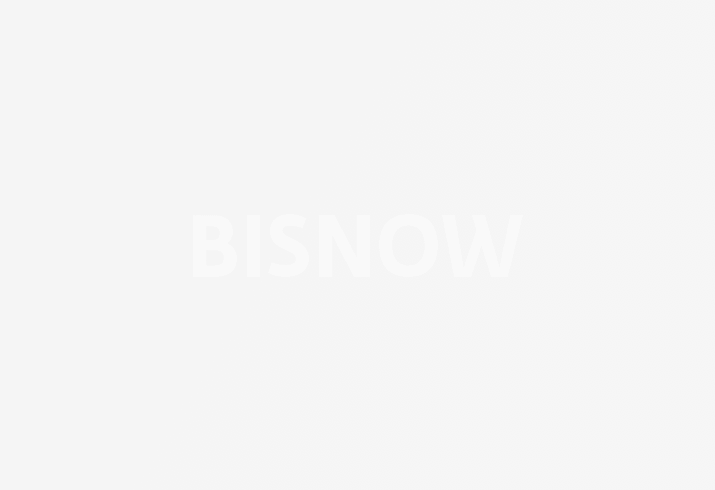
The Bay Area is a leader in the biotech industry, and design innovations here will impact how labs are built throughout the country. These biotech centers are adding more high-end amenities, sustainability and flexible design to create better research and innovation centers that meet the needs of researchers.
Amenities have been among the biggest trends in life science design, according to SmithGroupJJR Vice President Suzanne Napier.
“Amenities are really critical in the private sector and are taking some cues from academia and tech,” Napier said.
Fitness centers, entertainment centers, cafés, conference centers and services are all becoming a part of life science campuses. SmithGroupJJR has worked on space within the Lawrence Berkeley National Lab, UC Berkeley and for the University of California San Francisco as well as private centers like EmeryStation East.
The Bay Area’s weather has provided additional opportunities for outdoor amenities.
“In California, you can be outside so many months out of the year,” Napier said.
The weather has allowed for more outdoor space, quads, landscaped space and rooftop terraces and balconies for people to take a break outside, she said.
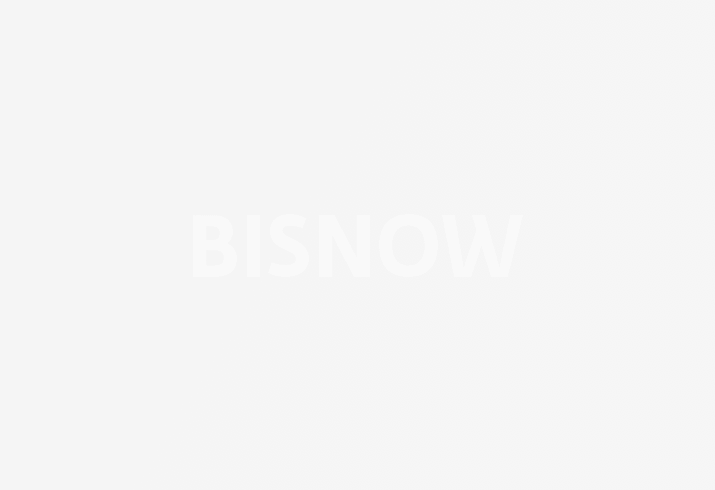
More natural light is being incorporated into these labs. About 20 years ago, clinical work was done in labs with no windows that looked like top-secret facilities. Now there is more glass and natural light and amenities, according to City of South San Francisco Director of Economic and Community Development Alex Greenwood, who spoke during a recent Bisnow event.
Sustainable design features are being added to R&D space to address the health and wellness of employees. Wet-lab researchers, who often deal with chemicals, drugs and biological matter in liquid or volatile stages, are getting more space outside of the harsh environments to maintain better wellness, according to Napier. Labs are also incorporating more flex space.
Labs are becoming smaller and are focusing on the right size needed for the work. This has meant tech research stations are moving into more traditional office spaces that have separate HVAC system requirements and are more energy efficient.
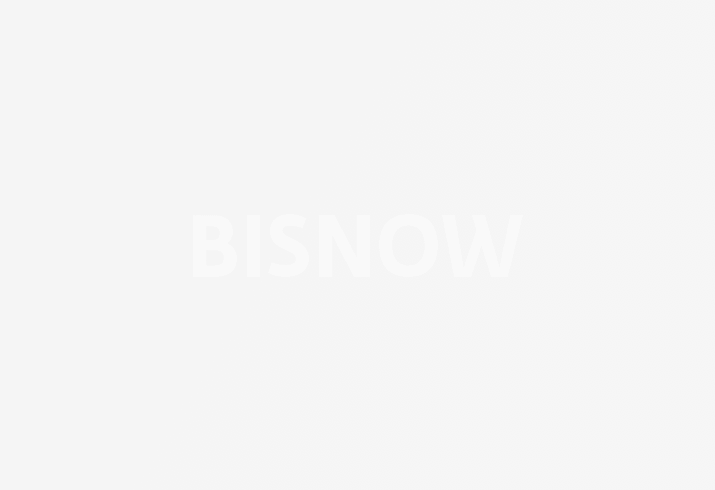
Design also is incorporating the demands of multiple disciplines. Different sciences are merging and sharing space, and there are no longer siloed R&D spaces, Napier said. The National Institutes of Health no longer funds basic sciences, which has helped push the industry toward multidisciplinary research.
With multiple disciplines occupying one building, designers and builders have to make sure each floor accommodates the needs of the specific scientists. Whereas biology researchers need more wet labs on the floor, chemistry researchers need more ventilation to handle fumes, according to McCarthy Building Cos. Vice President of the Northern Pacific Division Paul Erb.
Companies also are incorporating robots and aspects of artificial intelligence, which also will impact design. AI and robots that can be used to crunch data or handle unsafe chemicals can be outsourced to research hubs outside of urban cores, creating two distinct locations for R&D, according to Napier. Human hubs would remain in urban areas, while AI and robots can be moved to off-site locations.
How The Labor Shortage Is Impacting Life Science
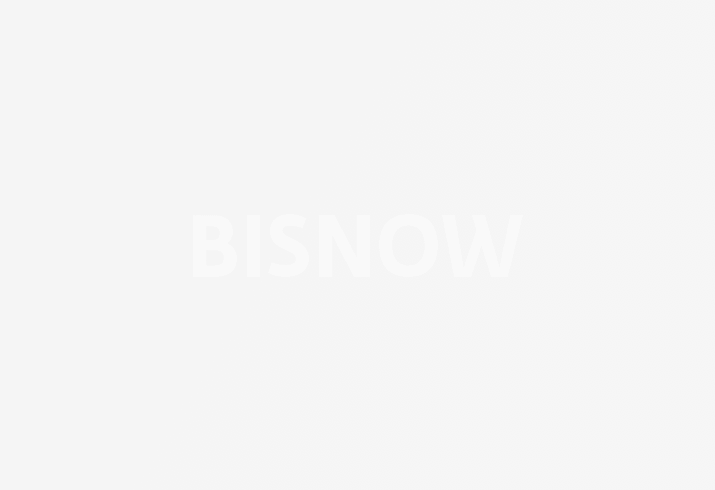
The construction labor shortage is impacting how builders approach life science design.
“Everyone is building and putting a strain on materials and labor, which is increasing across the board,” Erb said. “The bioscience market has only a finite number of suppliers providing specialty equipment.”
The construction company will get an idea of what clients want early on in the design process to secure better pricing and increase turnaround on delivery instead of contacting vendors when they might have a backlog, he said.
McCarthy Building Cos. will look at prefab with every project. It is currently using it with student housing, but it can be built whenever any aspect of a floor plan repeats. Prefab could be used in exterior skins for labs, for example.
“If we can fabricate off-site … and drop prefab into place, it requires less labor that is beneficial to clients and beneficial to costs and schedule," Erb said.
McCarthy also focuses on the mission of what clients want with their building to make sure the labs are fully functional and work for the client on day one. It offers a 60-day burn period after construction for the user to figure out if the lab works as intended before the space is open for business, according to Erb.
CORRECTION, AUG. 23, 3:09 P.M. PT: A previous version of this story did not have the official name for McCarthy Building Cos. The story has been updated.