Prefab And Modular Still More Promise Than Production In Bay Area
Modular construction, long heralded as a more efficient and cost-conscious method of construction, has yet to produce the promised cost and time savings and gain purchase in the commercial real estate industry, according to speakers at the Bisnow Bay Area Prefab and Modular Construction Conference at the InterContinental San Francisco hotel on July 27.
“It’s been full of promise for the entirety of my 32-year career, and it has yet to be realized,” Panoramic Interests owner Patrick Kennedy said.
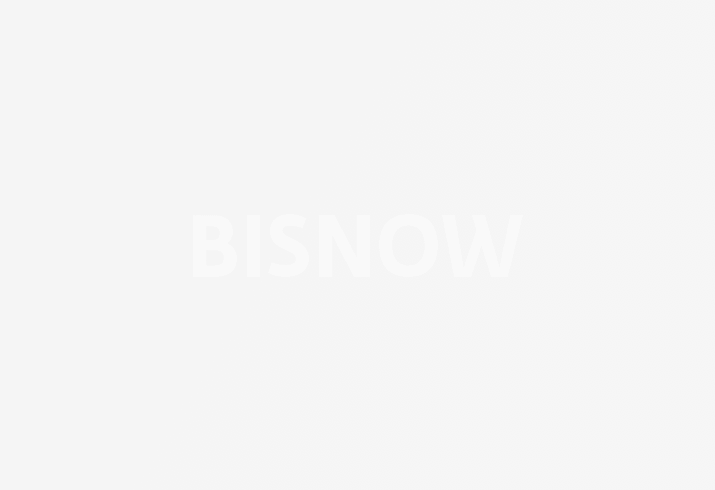
Kennedy was joined by others on the panel who expressed skepticism about prefab modular construction’s capacity to supplant traditional methods.
“We recently worked on a prefab project in Berkeley to create housing for the homeless, and we abandoned it last March because it just did not seem feasible,” Kennedy said.
One of the major constraints for modular construction in commercial real estate is the logistical challenges of assembling modular components in high-density urban environments.
Seven Hills Properties partner Luis Belmonte said he went to see a job after a modular construction company pitched him on its methods.
“It was in the North Bay, and there’s components spread over 3 acres,” he said. “Well, we don’t have 3 acres of staging at Mission and Cesar Chavez [in San Francisco], and I got a view of shutting down Mission Street and thought, ‘Well, we’re going back to stick because I can’t take the risk.’”
However, Lowney Architecture Design Director Mark Donahue said the modular method worked for the recently completed Moxy Hotel project in Downtown Oakland, partly because the logistics married well with the project schedule.
“It was an on-time delivery because the port of Oakland is right there,” he said. “So the modules come to the port and we had the staging area.”
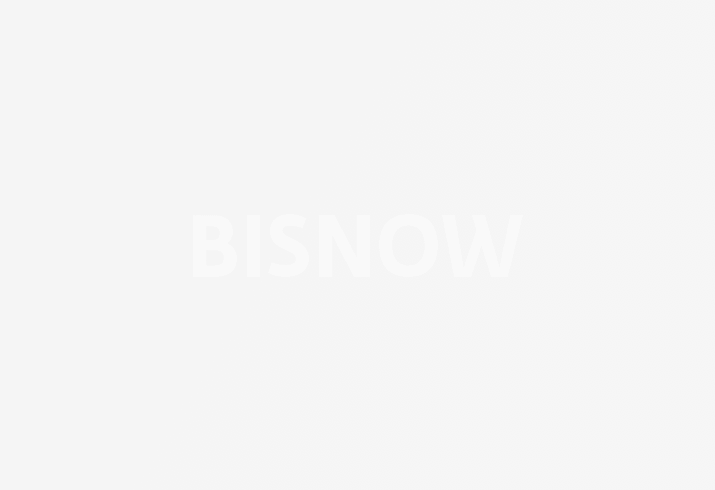
For other projects to realize the cost savings promised by constructing buildings off-site, precise planning for how to transport the modules to the site and deploy them almost immediately as they arrive is paramount.
“Sourcing the right staging area and having it close enough so that you don’t have your crane sitting idle because you’re dealing with traffic and trains is vital,” said Suffolk Construction Vice President Nick Schweiger, who recommended enlisting a logistics company with experience specific to modular construction staging.
The cost savings of building modules in a factory can also erode in other places, specifically if developers are working with mechanical, electrical and plumbing professionals who lack experience in connecting modular projects.
“MEP really does have a long way to grow in this industry,” Factory OS Vice President Andrew Meagher said.
Tidewater Capital Construction Director Kyle Winkler, who also worked on the Moxy project, said project directors must relentlessly focus on how to finish off the building if the efficiencies promised by factory build and a more streamlined permitting process are to be fully realized.
“Do not sleep on the back end of a modular project,” he said. “You have to finish vertical transportation, finish the corridors and you have to put your facade on, which takes about four to six months. If you don’t hit that, you won’t get the schedule savings.”
Many of the real estate professionals said that as more corners of the industry gain experience with modular construction, the promised time and cost savings will be realized.
“We’ve had more repeat trades that are on projects now,” said AO principal Nick Gomez, who added project directors are bringing more contractors into the factory to show them where connections are.
Even the skeptics on the panel said prefab modular still contains the promise that led many to predict it would take over the construction industry in short order.
“The times, they are changing, and I think the composition of this audience indicates that we are in a breakout time for a vast increase in the productivity of our industry,” Belmonte said.
Kennedy said that even if buildings aren’t entirely prefab modular, there is room for prefabrication of certain components to find more efficiencies.
“Stick by stick is not the way, but I don’t think box by box is the way either,” Kennedy said. “I think it’s somewhere in between.”