The Truth About Prefab: Dispelling 3 Common Myths
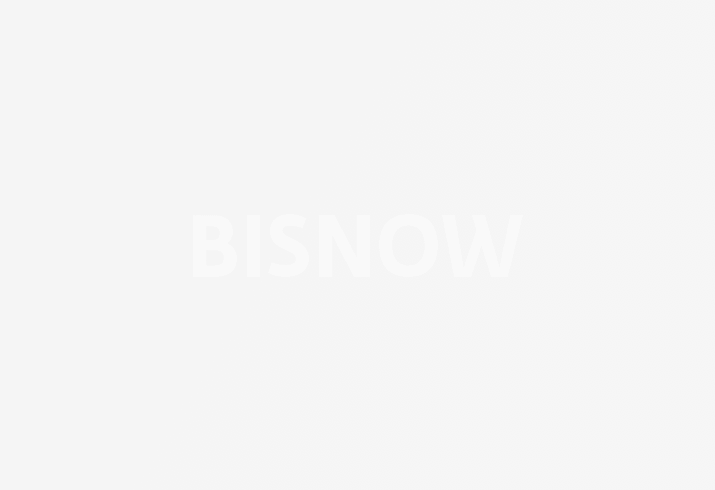
It is no secret that prefabrication, or prefab, has been growing in popularity. It offers many potential benefits, including cost, schedule and environmental savings. While prefab isn't a new method of construction, the evolution of materials and production techniques used over the past decade have grabbed the attention of property developers worldwide.
However, several misunderstandings and misgivings surrounding prefabrication have become de facto myths, including the notion that prefab and modular are one and the same. According to Blach Construction Development Executive Tony Mirenda, there are distinct differences between prefabrication and modular construction.
“To encourage owners and property developers to fully understand the benefits that prefab construction can offer, these myths should be effectively dispelled,” he said.
Myth 1: Prefab Is Modular
“All modular is prefab, but not all prefab is modular,” Mirenda said. “The term modular, specifically volumetric modular, describes either a specific element of a building or the entire building itself. All elements arrive on the project site ready to be assembled, much like a set of stacking cubes. Typically, there are design restrictions and little room for customization.
"Prefab, however, refers to the actual prefabrication of a portion or various portions of a building, which can be done both on- and off-site. While restrictions are always taken into consideration, customization is both common and feasible. Either way, modular and prefab each offer opportunity for cost and schedule savings.”
In short, prefab is the method of creating specific elements for a building in advance — not the entire building itself, but significant parts that together, along with other prefab, modular and/or site-built elements, make up the building as a whole.
Additionally, prefab takes myriad directions, Mirenda said. And contrary to popular thought, it isn't limited to framing. Prefab provides far more flexibility to designers than prescribed volumetric modular.
“While both prefab and modular are formulaic, modular dictates a very fixed way of building,” he said. “Conversely, prefab can be segmented, offering flexibility and the ability to customize various building components to meet the overall design intent.”
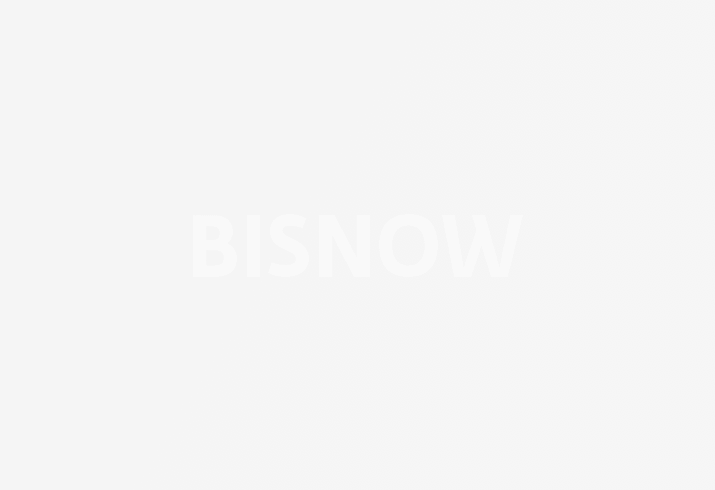
Myth 2: Prefab Is Low-Quality And Limited
Often, when people think of prefab, they picture the low-quality prefabricated homes from the 1960s. Today’s reality is very different, Mirenda said. Prefab extends well beyond residential construction, and while prefab components and modular buildings are often built manually, prefab techniques in general have come a long way.
“Prefab building components are typically fabricated in a controlled warehouse environment, which has a significant positive impact on quality assurance/quality control,” he said. “Precision technology can be employed for layout, cutting, assembly and so on. Not only does this result in high levels of accuracy but also stronger components that are made to endure the stresses of handling and transport.
"Moreover, workers, and subsequently productivity, are not affected by heat, rain or other weather extremes, ensuring consistent and safer working conditions.”
Those who might believe prefab is of lower quality might also believe timber is the only building material option, but this isn't the case, Mirenda said. There are a range of high-quality materials and systems alternatives, from precast concrete, light-gauge metal framing and steel to polystyrene foam and polymer/fiber-reinforced plastics — the latter of which are light, strong and durable.
Mirenda highlighted that each project has its own unique requirements. A pre-construction team can help dictate the success of a project from the earliest stages by identifying the right mix of materials and techniques, including modular or prefab.
“You need to know your local codes and environment: soil conditions, natural surroundings, seismic activity, weather, the neighborhood and the like,” he said. “If code allows, wood is a viable option, but in California, we’ve found light-gauge steel to be increasingly effective in many instances. Not only are there significant savings on project insurance, [but] light gauge steel also meets and can even exceed fire and seismic regulations. There is no one-size-fits-all solution in our industry.”
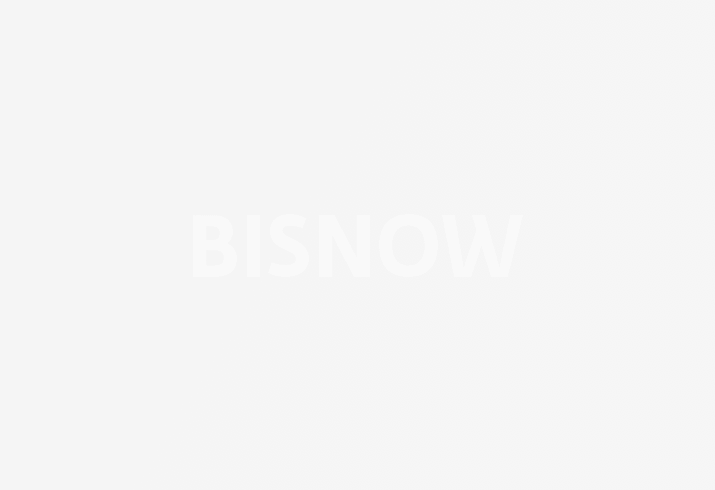
Myth 3: Prefab Is More Costly Than Modular
“Many businesses that offer modular construction claim it is 20% less in cost and 40% less in time,” Mirenda said. “But there are a lot of variables that can affect the cost-schedule savings paradigm.”
For starters, Mirenda said that since modular construction often lacks customization, other concessions and tradeoffs must be made that result in unplanned compromise, change orders, additional labor and subsequently increased costs. Alternatively, prefabrication, while seemingly more costly, offers better economies of scale.
“Yes, there might be greater costs to a builder upfront relative to equipment, for example, but at some point, the equipment pays for itself,” Mirenda said. “A key advantage, unlike on-site construction, is that the amount of labor required for prefabrication is typically known and planned for accordingly. Of course, changes can happen but are rare, so overall, prefab can be more cost-effective and predictable.”
Secondarily, as the popularity of modular has grown, so too has the pressure being put on factories. Any lack of factory space or shortage of materials can cause a delay, which can then cause a serious problem for a developer who has organized debt to pay for the deposit required by modular manufacturers. Prefab solutions, on the other hand, don’t generally involve a substantial upfront investment and are more agile.
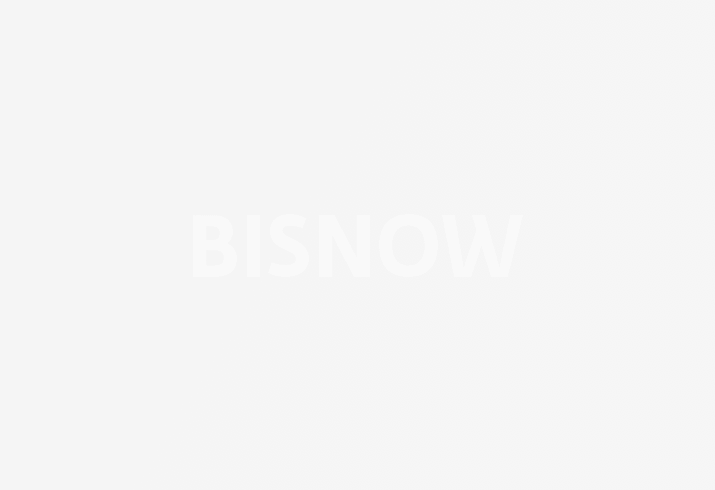
Finally, another benefit relative to cost savings is that various building components can be prefabricated on-site if space allows. This ranges from large-scale structural frames or trusses to smaller elements such as doorways or HVAC duct runs. And while workers may not be able to avoid rough weather or have the added benefit of large-scale robotics, on-site prefabrication reduces the need and additional time required to transport finished items.
“At the end of the day, substantial savings in construction result from concurrent project activities,” Mirenda said. “Huge efficiencies can be gained by prefabricating particular elements of a building, either on- or off-site, while simultaneously performing another task on-site. And if the project calls for it, volumetric modular components may be included as well, contributing to more efficient product delivery.”
Construction materials and building techniques are ever-evolving, and Mirenda said dispelling the myths long associated with prefabrication is critical to the future of building. Understanding the differences between prefab and modular could assist property developers in deciding if prefab construction can set their projects on the path to success — a path that may include some aspects of modular construction as well.
This article was produced in collaboration between Blach Construction and Studio B. Bisnow news staff was not involved in the production of this content.
Studio B is Bisnow’s in-house content and design studio. To learn more about how Studio B can help your team, reach out to studio@bisnow.com.