Related's Beachfront Fort Lauderdale Condos Highlight Construction Challenges For Florida Builders
When a crane crashed down mid-construction on the Auberge Beach Residences & Spa Fort Lauderdale during Hurricane Irma last fall, developer Related Group Vice President Patrick Campbell watched it happen. A downward thrust of wind, called a microburst, hit, and the crane began weather-vaning faster than usual.
“It collapsed on itself, and went through the sales center,” Campbell said.
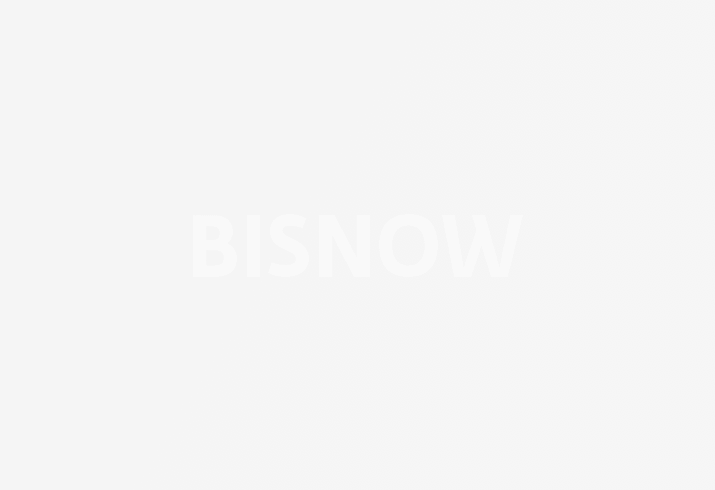
Although it took about two and half weeks to get the crane out — per regulations, the Occupational Safety and Health Administration had to do an inspection and clear the job site — and the hurricane ultimately delayed the project about 60 days, Campbell said that there was no lasting damage.
Construction of the Auberge highlights how Florida builders are adjusting to current challenges: a tight labor market and the looming threat of climate change.
The north tower, which is nearing completion, has only two units left for sale and the second tower, which topped off in late January, is about 70% sold, Campbell said. Two penthouses sold for $8.9M and $9.5M, respectively, record prices in Broward County.
The beachfront project, which has 171 units ranging from one to five bedrooms, is marketed as a “luxury development sitting directly on the sand.”
Campbell said the project is built on a resilient site. Compared to South Beach, where the base flood elevation is 6 feet above sea level, the Auberge site sits at 12 feet. Ground-floor slabs are elevated so that the building starts at about 15 feet above sea level. The road, beachfront highway A1A, comparatively, is at 9 feet. Campbell said Related follows federal regulations for building in coastal zones.
Moss Construction Vice President Alex Smith, who oversees construction on Auberge, said that on top of federal requirements, the state of Florida, to protect natural features like sand dunes, imposes certain rules for projects built within Coastal Construction Control Lines.
Construction crews built a seawall and incorporated some breakable construction materials, like breakaway walls, on the perimeter that are designed to detach in high winds, rather than compromise the whole structure. Local building departments are requiring that foundation systems be waterproofed.
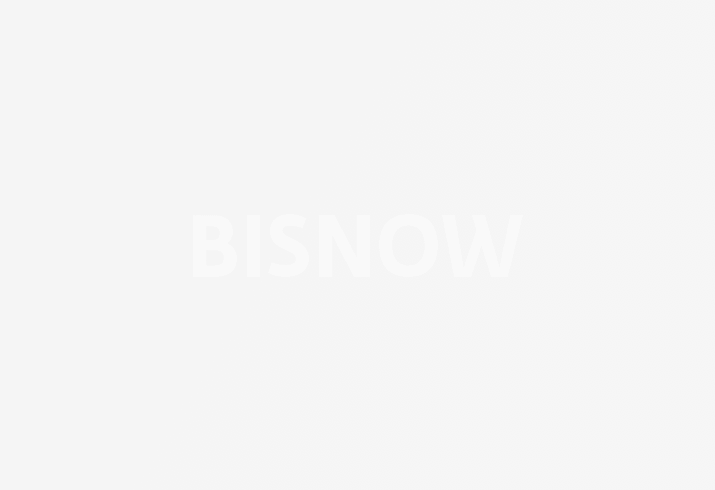
“I’ve seen that on the last three projects [I've done],” Smith said.
Auberge has a 120K SF underground basement that sits 15 to 20 feet below sea level. The foundation has a drainage system built into it, with a fully waterproof perimeter. These, along with the dunes providing a buffer from the ocean, protected the Auberge when Hurricane Irma hit, so that nothing got into the basement except regular rainwater, Campbell said.
In choosing its general contractors, Related does not ask for requests for proposals, Campbell said. The development team makes a shortlist internally and chose for the Auberge Moss, which had handled construction on other Related projects, including the SLS Lux in Brickell and Hyde Midtown.
“With construction costs going up, we couldn’t buy the job for what we bought it for now,” Campbell said.
Smith said the burden for making up the difference fell not on Moss but on its subcontractors. As the construction manager, Moss has about 20 employees on the Auberge site and uses various subcontractors for each specialized part of the job.
“The labor market is tough,” Smith said. “What we saw with Hurricane Irma is that 20 to 30% of the workforce left. We really didn’t get a lot of those individuals back. A lot of them went to Houston, where [following Hurricane Harvey], they could make $5, $6, $10 more an hour working. It really hasn’t recovered.”
Smith said Moss already had contracts issued with the subcontractors.
“They had to honor the contract values that they had. The subcontractors were obligated. If they need to pay an extra $5 or $10 to keep their personnel — I think that happened to a handful of them," he said. "There are not a lot of people on the sidelines not working. The workforce is thin for qualified personnel.”
A more frustrating problem, he said, was the cost of getting materials to the job site. Windows came from Colombia, but those were delayed two or three weeks until ports could get back on schedule, in turn affecting the workflow on site. His focus turned to expediting materials.
“That’s what keeps me up at night,” he said. “How can I get things done faster? How can I get things done better and more efficiently?”
For the first time, he used a total station robotic layout system — a combination hardware/software system.
“You load up the construction documents into it, and it helps lay out floors to one-sixteenth of an inch,” Smith said.
That proved helpful in executing Auberge’s unique design, with curved towers —one of which is like a semicircular staircase.
“We’re building on a radius, with each floor stepping back as it goes up the building. Each wall is really on a radial point," Smith said. "Not all walls are square; they’re pie-shaped. You can’t just go and use a tape measure.”
A certificate of occupancy for the north tower is expected in April. The south tower should be delivered in September. As for the broken crane, it is still undergoing forensic testing in an Orlando warehouse, and it remains to be seen whether the builder’s risk insurance policy or the crane company’s insurance policy will cover losses.
“The insurance companies are battling it out,” Campbell said.