In Virginia, 3D Printers Are The Latest Weapon In The Fight Against The Affordable Housing Crisis
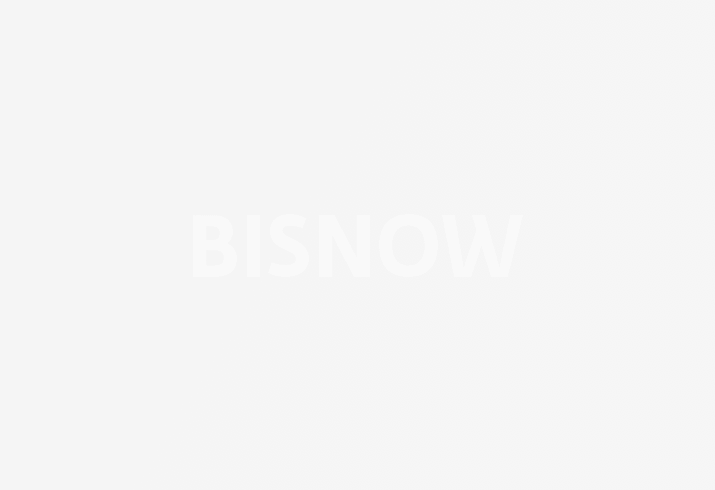
The U.S. is in the midst of an affordable housing crisis. Nationally, there is a shortage of more than 7 million affordable homes, and there is no state where a renter working full time at minimum wage can afford a two-bedroom apartment. In response to this crisis, some organizations are turning to innovative solutions to bring more affordable homes to their communities.
Virginia Housing is a nonprofit housing finance agency with a mission to help all Virginia residents gain access to affordable homes. In 2021, Virginia Housing created an Innovation Demonstration grant to help spur the adoption and utilization of new construction methods, building materials and processes to create more affordable housing inventory. The Virginia Center for Housing Research at Virginia Tech received a $500K grant enabling a 3D printer to be brought to Virginia from Denmark.
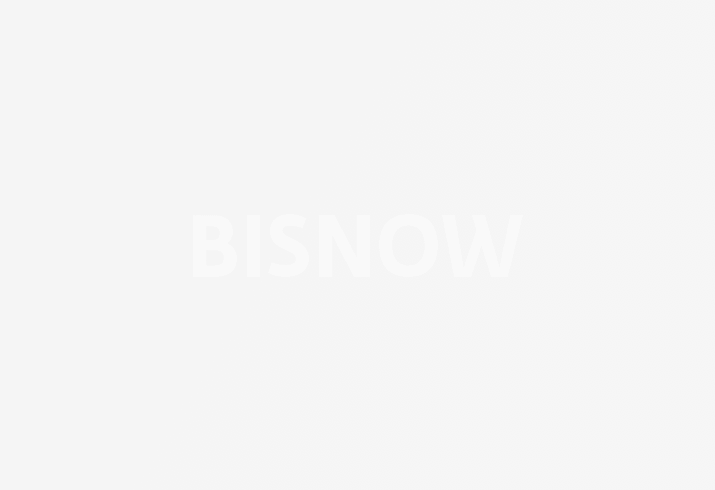
The printer was used to complete the first 3D-printed home in Richmond, which features three bedrooms and two bathrooms.
"The process of creating these walls resembles creating a layer cake, as the printer head travels along the layout for the walls, extruding a cement mixture, layer after layer, to build up to the desired wall height," Director of Strategic Housing for Virginia Housing Chris Thompson said. "The hope is that 3D-printed houses will be able to be constructed at a lower cost because they require fewer on-site resources and less time to build."
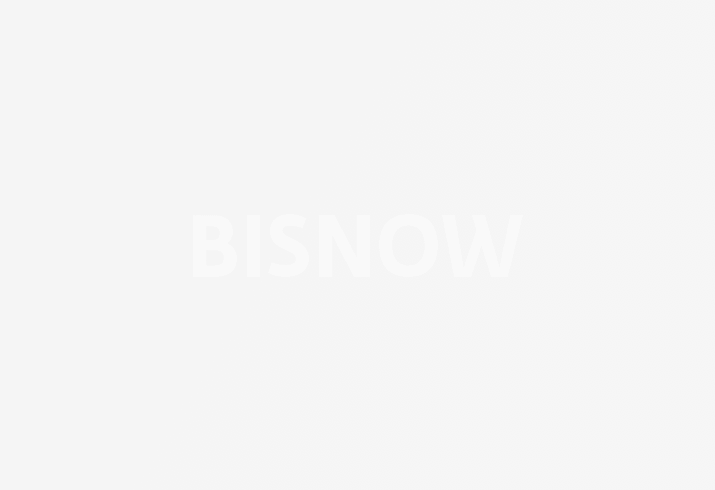
Additionally, Thompson said, these houses are exceptionally durable and energy-efficient, cutting back on repair and heating costs for homeowners.
This home is outfitted with smart home sensors called “Building Data Lite” —using Raspberry Pi hardware — by VCHR and monitors indoor environmental data including air quality, temperature, humidity, lighting, sound, vibration, smoke, gases and security.
Alquist, a 3D printing construction firm, handled the printing of the walls, while RMT Construction & Development Group served as the general contractor.
Additional partners included Better Housing Coalition, which helped fund the project through homebuyer assistance. Project: HOMES owned the lot where the 3D printed home was built, provided project oversight and worked with a local real estate agent to find an interested homeowner who met the income requirements. The two nonprofit housing organizations also coordinated local regulatory compliance, permitting, zoning and insurance.
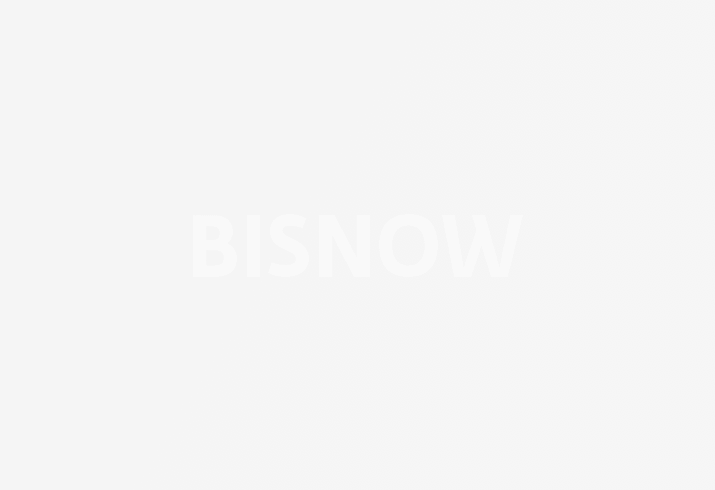
“Innovation requires looking at things differently – imagining the possibilities,” said Susan Dewey, CEO of Virginia Housing. “Because of this focus on innovation, 3D printing is now one of the many tools available to us to help increase housing inventory. And, we’re not going to rest on our laurels. We’re going to continue to find new solutions to the affordable housing crisis.”
Studio B is Bisnow’s in-house content and design studio. To learn more about how Studio B can help your team, reach out to studio@bisnow.com.
This article was produced in collaboration between Virginia Housing and Studio B. Bisnow news staff was not involved in the production of this content.