Elevated Prices, Labor Shortages Aren't Going Away. Now Construction Needs To Adjust
Necessity is the mother of invention, the saying goes. There are few sectors in the U.S. economy that embody that old cliché more than the construction industry right now.
Between labor shortages and supply costs, lagging supply chains and rising interest rates, there are more than a few factors pushing against the development pipeline. But a few of those factors may be especially sticky, pushing developers, contractors and construction companies to rethink how they do things.
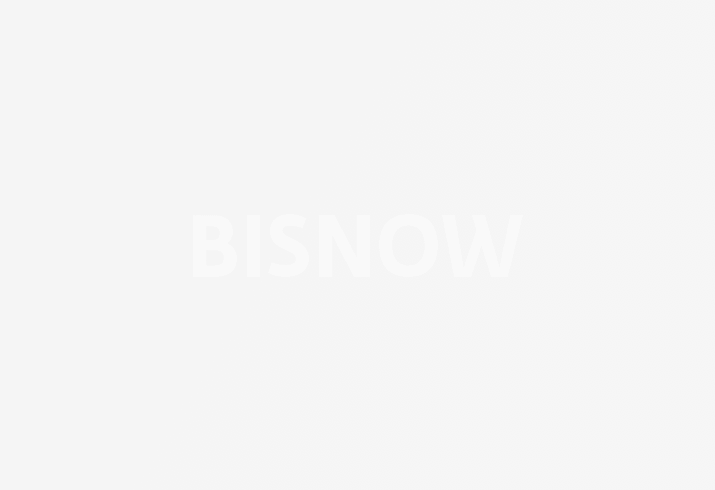
While restrictive interest rates might not be around for the long haul, construction's labor supply woes and high material costs may not get much better, panelists said at Bisnow’s Construction and Development event at the Washington Marriott Capitol Hill Wednesday. Those sticking points, they said, make creativity more important than ever.
"I get the question frequently about when are prices going to come down, and unfortunately, I’m not sure they ever will," DPR Construction Northeast Commercial Core Market Leader Matt O’Malley said. "I mean, that’s just how our industry works."
In 2022, the construction industry had on average more than 390,000 openings per month, the highest level on record, according to a February study from Associated Builders and Contractors. ABC projected that the industry would have to add more than half a million workers on top of its normal hiring pace to meet labor demand in 2023. And as the construction population ages, that makes the need more necessary.
“With nearly 1 in 4 construction workers older than 55, retirements will continue to whittle away at the construction workforce,” ABC Chief Economist Anirban Basu said in the report.
High Concrete Group sales representative Eric Rowits said his company sees labor as one of its most significant challenges.
“Labor is tricky because what we’re seeing is probably for every 10 folks that retire or leave our industry, it’s only replenished with two, maybe three,” Rowits said.
Jair Lynch Real Estate Partners Director of Development Kaleena Lee said that as developers wait for interest rates to drop to start construction, the rush to develop could additionally strain the already-tight labor market.
“We’re all bullish about some starts in ’24 and many more starts in ’25,” she said. “But if we all start at the same time, we’re all pulling from the same labor pool.”
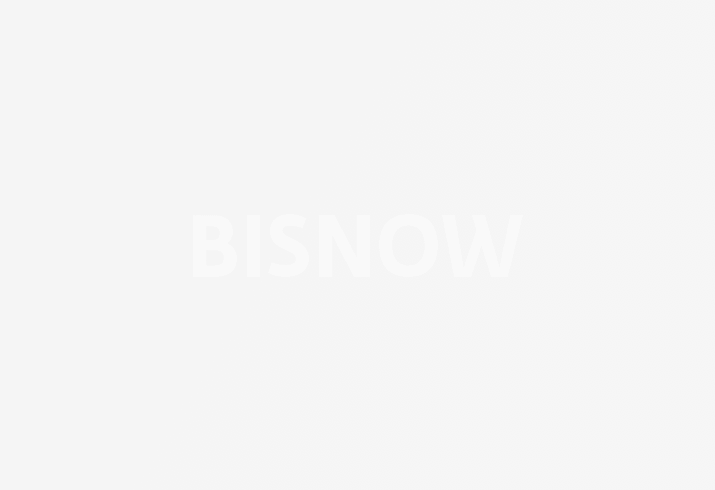
Meanwhile, as of June, construction costs were up more than 38% since the start of the pandemic, more than twice the economywide increase over that span, according to ABC.
"Prices, once they go up, they just tend to not go down," DPR's O'Malley said. "So I really don’t think planning on a big reduction in cost, that’s gonna save the market. I think we have to sort of bake these things in as this is where the new normal is for construction."
Those costs are straining projects across the board, even for a well-capitalized company like Toll Brothers, said Erin Reisinger, a senior director for Toll Brothers Apartment Living. Even though the publicly traded developer has a “very robust balance sheet,” she said construction costs present a stumbling block.
“We are still seeing projects get shelved because we can’t meet those higher return thresholds that equity partners are looking for.”
Given the costs and labor shortages, panelists spoke about ways they are reimagining their processes and balance sheets to make projects pencil.
“We’re starting to look very early on at ways we can reduce costs,” Reisinger said.
She said Toll Brothers is looking at ways to maximize efficiency in the construction of its multifamily developments, working to minimize gross square footage while maximizing rental space. That includes looking at underutilized amenity spaces and transforming them into rentable square footage.
“Can we take that makerspace and create a unit that’s going to produce income?” she said.
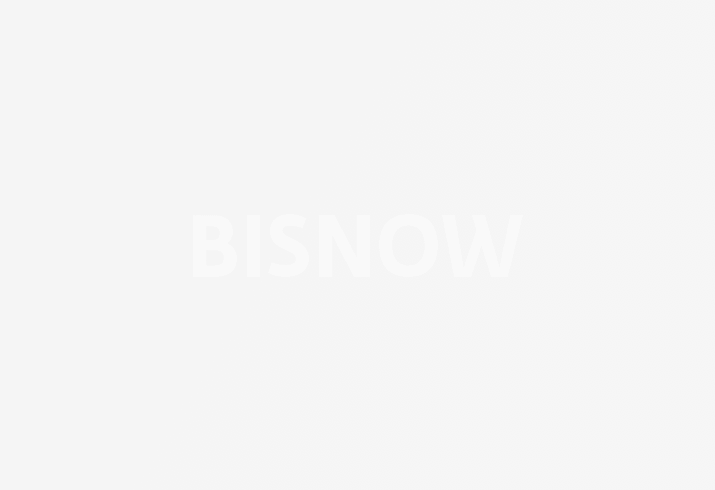
High Concrete Group, which makes precast concrete, is using technology to assist with the skilled labor shortage, Rowits said.
“We found that introducing technology really limits the amount of skilled tradesmen that are in our buildings,” he said, describing how the company provides Ikea-like instructions via tablets and TVs.
“Individuals can just show up and put all the pieces and parts together and may not have to pick up a tape measure to actually figure out how the length and square works and how the panels are assembled,” he added.
Eastern Atlantic States Regional Council of Carpenters Senior Council Representative Michael Connor described his company’s four-year free training program accredited in Maryland, D.C. and Virginia, where apprentices can learn skills as they earn a wage.
HITT Executive Vice President Josh Foresco said construction companies need to do more research and development to look at improving ways the industry functions.
"As an industry, construction spends less than 1% of annual revenue on R&D and improving the way we do business," he said. "When you look across all the industries out there, it is a paltry sum of money."
Foresco said HITT has a contingent going to Japan in a few months to look at how to advance prefabrication, which he hopes will "pump a shot of vitamin B12 into the process that we’re taking, and the U.S. economy is taking, in construction."