The DIRTTy Little Secret Behind High-Quality, Low-Cost, Efficient Interior Installations
If you still think construction and technology are about as compatible as oil and water, it’s time to reconsider.
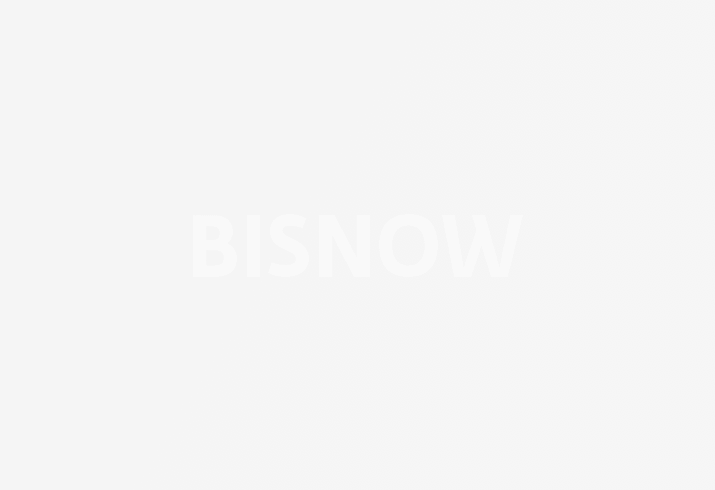
True, hard-hat designated zones seem hardly hospitable to fragile hardware, but innovative, forward-thinking construction and design firms are taking advantage of modern fabrication techniques and associated software. Implementing highly integrated, sophisticated technology not only gives firms a competitive edge, pumping adopters’ bottom lines, but also produces more precise, high-quality results.
Intellistruct—a sister brand to Bialek Environments, a full-service provider of contract office furniture and design services—harnesses powerful technologies in concert, teaming with DIRTT and ICE to grow into virtual reality for the built environment.
Their main partner is DIRTT, whose prefabrication techniques are Doing It Right This Time. The process helps Intellistruct achieve client and design partners’ intent with quality and consistency, mitigating delay risks with industry-best lead times and fast on-site installation.
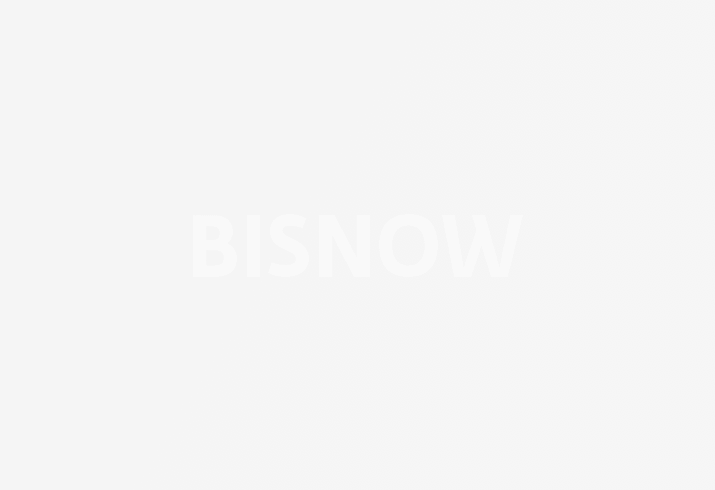
The plug-and-play nature of DIRTT interiors is just one aspect of its main selling point: seamless integration. They create easy access for power, data and A/V infrastructure and support any manufacturer’s furniture, storage and millwork with pre-blocked walls and “antlers” for hanging bracketry.
The increase in workflow efficiencies can cut Intellistruct’s delivery schedule by 15% to 20%, with fewer project management and general conditions costs.
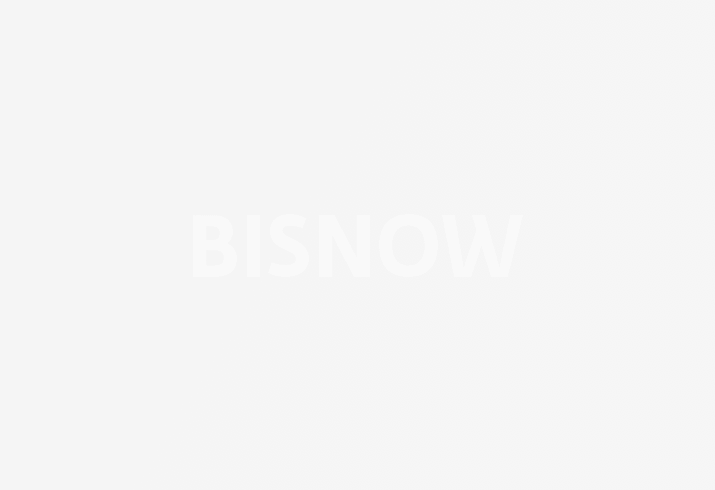
DIRTT construction reduces the need for floor leveling, halves trash hauling volume, decreases construction waste by 65%, curbs damage to architectural finishes by 65% and saves 5% to 12% overall in construction costs, including labor and materials, according to third-party input from Liberty Mutual.
DIRTT uses ICE building information model software, which provides clients an interactive, virtual walkthrough of their design and furnishings, so they can visualize the space and more closely tailor it to their needs.
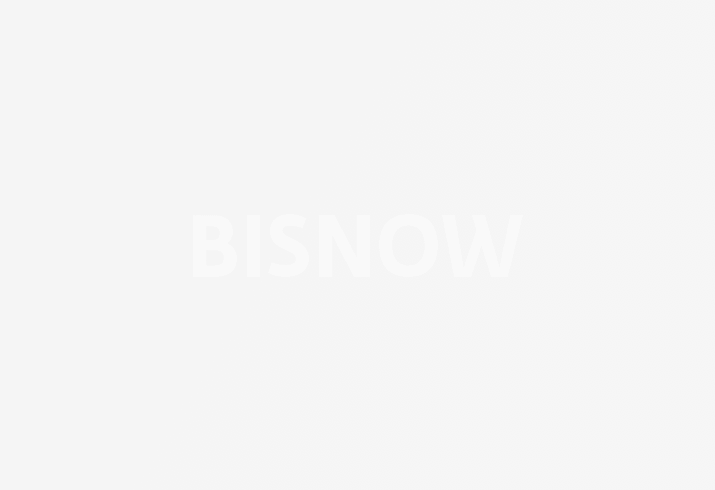
By navigating and experimenting with a computer-generated rendering ahead of time, clients avoid costly delays and headaches created when elements installed are found to be unsuitable.
Clients can forgo deciphering cryptic line drawings and site plans, as ICE updates the user-friendly 3D rendering in real time while pricing and manufacturing schedules are automatically churned out.
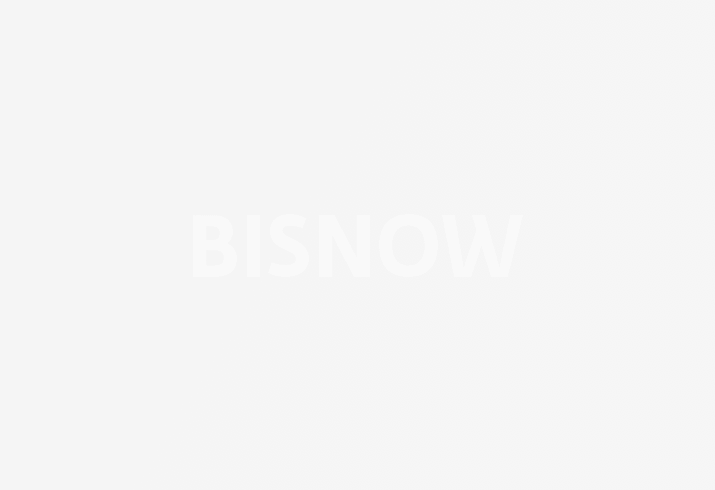
The natural evolution of this crucial technology exists within the hot-topic realm of virtual and augmented reality. Clients can actually “walk” around the space, either through Oculus Rift’s handheld controls or with the HTC Vibe’s hands-free tracking system.
“It’s an extremely compelling experience for the participant,” says DIRTT CTO and co-founder Barrie Loberg, mentioning the new technologies’ ability to keep viewers from feeling the vertigo that used to be associated with VR.
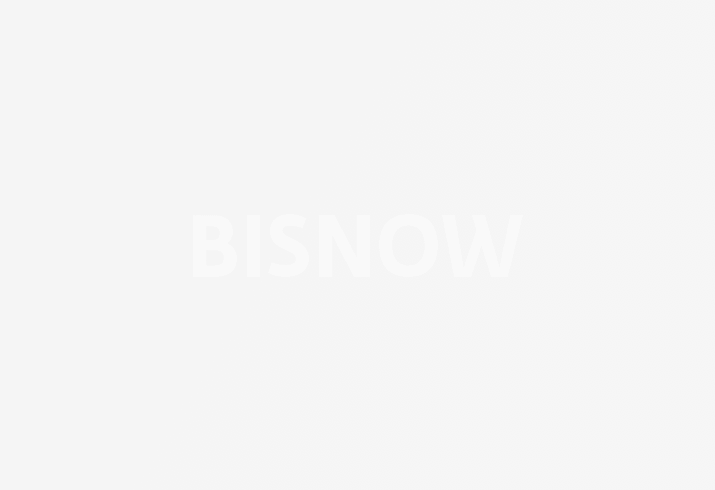
He also says he’s experienced firsthand countless clients discover issues and solutions with the VR tech that otherwise would have gone unnoticed until it was too late.
DIRTT, ICE and VR have demonstrable benefits for construction. To learn more about an early adopter and Bisnow content sponsor, click here.